Fluid levels are measured in various water bodies such as rivers, wells, or tanks, or other fluid containers, using pressure transmitters, among other techniques. The principle of pressure transmitters, when used to determine fluid levels, is as follows: the pressure at the bottom of a fluid body is proportional to the height of the fluid above it. This is the hydrostatic head pressure, and is measured by the transmitter to obtain the fluid level reading. For accuracy of measurement, the transmitter must be placed at the lowest point, that is, mounted on the bottom of the container.
Specific gravity is another constant which should be factored into the equation as below, to calculate the level of fluid:
Where
H = P/SG or P=SG • H
H – Height of the liquid being measured (usually in inches, centimeters, meters, feet and so on.)
P – Hydrostatic head pressure at the bottom of the tank (usually in inches of water column, feet of water column, bar, psi, Pascal’s, etc.)
SG – Media’s specific gravity (a dimensionless number calculated from: Density of media being measured ÷ Density of water at 4 °C. For instance, the density of kerosene equals 0.82 g/cm3. Therefore, the SG of kerosene is 0.82 g/cm3 ÷ 1.00 g/cm3 = 0.82
To consider an example, if a vessel contains water to a depth of 8 inches, the hydrostatic pressure at the bottom of the container is calculated as follows:
H = 8 inches of water
SG = 1
P = x PSI
P = 1 • 8 inches = 8 inches W.C. (water column)
That is, the hydrostatic pressure P at the bottom of the vessel is equal to that of an 8-inch water column.
1 inch of W.C. = 0.03613 PSI (27.678 inches of W.C. = 1 PSI).
8 inches WC • 0.03613 = 0.289 PSI
So 8 inches WC = 0.289 PSI of hydrostatic pressure at the base of the vessel.
It is obvious that the level measurement is affected by variables such as the specific gravity, the location of the device, the temperature and the gas pressure, the last two of which act upon the fluid when it is in a sealed tank to materially alter the result.
Types of Vessels in Which Fluid Levels are to be Measured
Different techniques must be adapted for use in determining fluid levels in various settings.
Vented Tanks
The simplest setting for fluid level measurement is the vented or open tank, which includes elevated, underground or above ground tanks which are provided with openings in the form of vents, or in any way allow the medium to communicate with the local atmospheric pressure.
The fluid level sensor is usually mounted on the side of the tank as shown in Figure 1, but a probe may also be submerged in the medium as shown in Figure 2. The hydrostatic head pressure is measured and used to calculate the level accurately.
.jpg)
Figure 1. Vented/open tank with a Tri-clamp mounted transmitter.
Suppose the fluid level is to be measured in a vertical tank which is 20 feet in height. If the fluid contained in it is water, this means the maximum hydrostatic head pressure would be 20 feet of W.C. at 4 °C when it is full.
1 foot of W.C. = 0.43356 PSI
So the maximum hydrostatic head pressure on the base of the tank and therefore on the pressure transmitter is 8.671 PSI.
.jpg)
Figure 2. Open tank with a submersible transmitter.
.jpg)
Figure 3. Insulated tank with adapter.
In a different setting, if the tank is filled with kerosene instead, which has an S.G. of 0.82, the equation would now read:
P = 0.82 • 20 feet = 16.4 feet water column or 16.4 feet • 0.43356 = 7.11 PSI.
The difference in hydrostatic head pressure between 20 feet of water and kerosene is 1.561 PSI or 3.6 feet WC. This is significant, showing how important it is to know the S.G. of the medium being measured to get a precise level measurement.
Some factors to be taken into consideration in selecting a pressure transmitter in such a setting include:
- Is it possible to tap the bottom of the tank? If not, is it possible to put in a level probe from the top of the tank?
- Is the use of a weld-in adapter possible?
- What types of fitting are suitable for use in the vessel being considered?
- Is the measurement part of a sanitary application which requires prior approvals for the use of certain products, or where contamination is absolutely not permitted?
- Is the medium compatible with the standard sensor materials or will it be necessary to obtain additional optional wetted components?
The Viatran model 359 is a robust sensor suitable for use in fluid level measurement even in a sanitary application or if the instrument has to be fixed or adjusted from the outside of the tank. A further advantage is the availability of a variety of receivers for this model, which allows the end-user to either select one which suits the present setup, or to use welding adapters to fit one of them on if a new installation is being put up.
In the case of a non-sanitary application, the Viatran model 517 offers the advantage that it can be simply lowered into the vessel from the top. This offers the easiest route for measurement, without the need for making holes or using adapters to fit it to the orifices in the tank wall. Moreover, its removal is also a straightforward procedure and can be accomplished without the need to empty the tank first. Alternatively, models 244, 344 or 544 are all capable of being plumbed by a pipe fitted to the base of the tank or vessel.
The use of an insulated tank means that a special adapter must be welded flush on the wall of the inside of the tank, penetrating the entire wall thickness to reach the outside, where the transmitter is attached to it.
Sealed Tanks
A sealed tank has a pressure blanket of gas on top of the fluid level inside. Thus the pressure at the bottom of the tank is the sum of the hydrostatic head pressure and the gas blanket on top. This makes it harder to measure the liquid level as precisely as in a vented tank since correction must be made for the pressure contribution of the gas blanket above the liquid.
The most accurate of several techniques devised for this purpose is the use of differential pressure (DP) transducer. This avoids the addition of the gas pressure. As shown in Figure 4, a DP has one high and one low leg. When the higher leg is at the base of the tank and the low leg is attached to the part of the tank that is above the fluid level. Thus the transmitter measures the difference between the total pressure at the bottom and the gas pressure at the top, enabling it to read off the liquid level alone. In this situation, barometric pressure is irrelevant.
.jpg)
Figure 4. Sealed tank with a differential pressure transducer.
.jpg)
Figure 5. Vented tank with changing media density.
In the use of this technique, however, several factors must be accounted for before it is applied:
- Will both legs be at the same temperature?
- What is the optimum length of each leg?
- What is the best location for the transmitter?
- What should be the maximum and minimum temperatures for the medium and the gas blanket?
- Will the system be located outdoors or indoors?
- Will the tank ever experience a vacuum?
For the sake of illustrating the use of this type of measurement, we may assume a tank 30 feet in height, containing 20 feet of water (with a head pressure of 8.671 PSI), and a blanket of pressurized gas at 5 PSI above the fluid level. Since water has an S.G. of 1.00, the total pressure (hydrostatic head pressure plus gas pressure) reading at the bottom of the tank would be 5 PSI + 8.671 PSI = 13.671 PSI or 31.539 feet W.C.
Figure 4 shows the use of two seals for this purpose, connecting the two sides via capillary tubes filled with oil. The side of the DP which is lower is fixed at a point which is above the 20 feet mark and in the gas-filled area, and will sense the 5 PSI of the gas blanket. The high side is fixed on or as near as possible to the base. The DP will find the difference between the combined pressure on the high side (at the tank base) and the pressure sensed on the low side which senses the gas pressure, leaving 8.671 PSI or 20 feet W.C.
Another option is the use of a set of two transmitters as detailed below. This method allows for the measurement of the fluid level, but with slightly less precision First, the Viatran model 517 is lowered into the sealed tank. The other end is passed out through a sealed feed-through exit orifice. A vent is not needed if model 517 is used in this type of situation. In combination with the 517 model, another transmitter such as the Viatran model 570 is mounted at the top of the tank to measure the pressure exerted by the gas blanket alone. The signals from each of these transmitters are now fed into a circuit which finds and displays the difference between them, as a reading of the fluid level. The results are typically within the acceptable range of accuracy in situations where space for installation is at a premium.
Vented Tanks with Changing Media Density
A situation may exist when the same tank is used to harbor different media at varying densities, or when the medium changes density during a process. Such is the case in the food and beverage industry because of mixing and blending of various ingredients in a single tank. Gage-type instruments cannot be used alone in such a setting with any acceptable degree of precision.
On the other hand, gage transmitters may be used along with a DP to obtain accurate readings of the fluid level in a situation of varying medium density. Figure 5 shows this type of setup, where the high and low legs of a DP at a specified distance between them, to measure the hydrostatic head pressure. Once the S.G. of this medium is measured, this can be multiplied by the reading of the level from the gage transmitter to obtain the actual fluid level.
For instance, if the tank is 30 feet in height and has 20 feet water, a DP may be fixed on one side of the tank with the low leg positioned precisely 12 inches above the high leg. The pressure differential will then be 12 inches W.C. or 0.43356 PSI. Using this as a foundation, the S.G. of other liquids can now be calculated.
In the present example, if the tank contains an unknown fluid instead of water, and the DP output now corresponds to 9.84 inches W.C. when the legs of the DP are 12 inches apart in height, the following formula is applied:
SG = DP/D
DP – Reading from the DP of the distance between DP legs (9.84 inches of water column)
D – Actual distance between DP legs (12 inches)
SG – Specific gravity
So:
SG = 9.84 inches/12 inches
SG = 0.82
Here, the specific gravity of this media is equal to 0.82.
Now the corrected level of the medium can be calculated from the present density, by multiplying it with the output signal from the gage-type Viatran model 359 transmitter mounted at the bottom of the tank. In the current example, 20 feet W.C. is multiplied by the S.G. of 0.82, or 20 feet W.C. times 0.82 = 16.4 feet W.C.
.jpg)
Figure 6. Sealed tank with changing media density.
A host of input devices are now available to multiply these two 4-20 mA outputs and show a final 4-20 mA output that is equivalent to the corrected level reading. Thus the correct liquid level can be measured even when the media has fluctuating density.
Sealed Tanks with Changing Media Density
In a sealed tank which is, by definition, under pressure, but also has medium which is of changing density, two DP transmitters may be used to obtain an accurate liquid level measurement.
The first DP (DP1) is mounted such that the low leg is within the gas blanket area, while the high side is at the base of the tank, and thus senses the combined pressure of the liquid and the gas blanket. The output from DP1 is thus the static pressure measurement alone.
A second DP (DP2) is fixed with the high and low legs positioned exactly 12 inches apart, on the side of the inner wall of the tank. The S.G. of the medium is now calculated, and multiplied by the static pressure. This yields an accurate figure for the fluid level.
Final Recommendations
Thus Viatran offers a full range of pressure transmitter solutions which can be combined in various ways to arrive at the solution that is appropriate for the measurement of liquid levels using different techniques. These include models 274, 374, 276, 376, 571, 574 or IDP10, which are capable of measuring within a range of 0.5 inches WCD to 3000 PSI. They also come with a full range of optional accessories such as capillary tubing, remote seals, and fill fluids for every type of application. The Viatran model 517 is another offering which combines ease of set up with impressive accuracy. On the other hand, if sanitary applications are in mind, Viatran models 350, 351 or 359 are recommended.
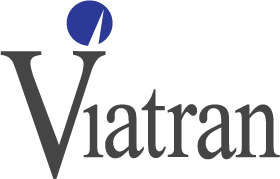
This information has been sourced, reviewed and adapted from materials provided by Viatran.
For more information on this source, please visit Viatran.