Before LNG or LPG can be employed as a source of energy or in production for the petrochemical or chemical industry, it must be put through a complete series of process stages.
.jpg)
Image Credit: VEGA
These are to take away undesirable elements, for example, mercury and sulfur, along with refining it to ensure the calorific and quality requirements are achieved; before transport, compression, and subsequent use.
Through all these process stages, dependable level measurements are essential for the smooth and safe functioning of the plant.
There are physical characteristics of LNG or LPG, which can also be different corresponding to the medium composition.
This can be a result of its refined state, supplier, origin, along with variations in ambient and storage conditions.
Many measuring concepts fail to provide a dependable, accurate measurement with no need for recalibration because of this. Mechanical measuring techniques are known to be likely to malfunction and need maintenance.
.jpg)
The radar sensor for liquids VEGAPULS 6X (flange version) is ideally suited for poorly reflecting media, i.e. liquids with small DK values.Image Credit: VEGA
Contactless radar technology is the measuring technique of choice for these reasons. LNG/LPG also has a very small dielectric constant and a low density (which influences its reflectivity to microwave-based radar measurement systems).
This has meant historically that special installations such as particular radar configurations and stilling tubes were a prerequisite for reliable function.
They also must be able to cope with poor reflections, internal fittings, isolation valves, and often turbulent surfaces. These have even displayed some reliability challenges for radar in the past.
Poorly Reflective Media
Utilizing a level radar with a signal frequency such as VEGAPULS 6X with 80 GHz technology, it centers the radar beam over three times more narrow and concentrated than radar level sensors before.
This makes it especially well-adapted to poorly reflective media, for example, compressed liquids or gases with small dielectric values common in this industry.
A more concentrated signal makes sure that a good reflection is attained, while superior sensor sensitivity can distinguish the smallest reflection from a distance even in the presence of surface turbulence.
.jpg)
VEGAPULS 6X measures the level in a cooling system on board a gas tanker. Image Credit: VEGA
The exceptional focusing ability makes the measurement more accurate and reliable. The level transmitter is also more cost-effective to design and perform.
To help with this, it is available in a range of alternate antenna sizes and systems. The connection sizes currently (with beam angles in brackets) on offer vary from ¾ " (14 °), 1½ " (7 °), DN50/2 '' (6 °), and DN80 '' (3 °).
When it comes to any challenging internal fixtures, the focusing feature has one advantage that is the most obvious: the narrow measuring beam can easily avoid any internal tank installations and components, but even more benefits can be seen.
The Isolation Valve Challenge
The strict standard that every sensor must be separated from the system utilizing a valve fitting is common in the industry.
This must be accomplished without disturbing the process, for example, not shutting down the production equipment or part of the system. This need is critical for the majority of liquid gas tanks.
For a radar level sensor, this means that it must be mounted on a ball valve. The intention of this is to ensure that the sensor can be removed from the process, even when the operation is ongoing.
The installation of a radar sensor on a ball valve was not recommended beforehand, as the ball valve itself creates large interfering reflections in the close range.
This is because of reflections at internal valve seating and sealing points, along with process connections such as gaskets and flanges.
These close range and small signals are produced inside the throat of the ball valve. They subsequently multiply and feedback interfering signals, which frequently and directly obstruct the sensor’s measuring path.
Dependable measurement with radar through a ball valve was frequently impossible in the past or highly limited, particularly in liquids with small dielectric values.
The impact of the ball valve is much smaller again due to the significantly enhanced sensor signal focusing on the VEGAPULS 6X.
The ball valve creates no obstructing echoes as a result. Impeding signals in the close range are avoided and a dependable measurement is ensured.
A further advantage for the user is that the sensor can be installed on longer nozzles and onto existing shut-off devices, which keeps retrofitting costs to a minimum.
.jpg)
VEGA sensors can reliably and accurately detect even the lowest levels of LNG at the bottom of a tank. Image Credit: VEGA
Better Utilization of Tank Volume
VEGAPULS 6X also has a beneficial influence when measuring liquids with small dielectric constants at low levels near to the bottom of a tank. Radar signals are reflected at the medium’s surface.
In the case of liquids with small dielectric constants, certain signals reach through the medium and are then reflected by the highly reflective, underlying bottom of the metal tank.
Two signals are detected: the weaker actual liquid level and the stronger one from the bottom of the tank. The smaller the dielectric constant of the medium and the lower the level, the greater the signals from the tank bottom become.
This can mean that the unit either has incorrect readings or prematurely ‘jumps down’ to zero levels before being empty.
As a result of the extensively shorter wavelength of the 80 GHz signals from VEGAPULS 6X, the signals that reflect back are much greater in strength. Any that do penetrate the medium surface are strongly attenuated (much more than with radar sensors before).
Any undesirable reflections from the vessel’s bottom are much weaker as a result. This means that the liquid level signal reflected back continues to be stronger than the undesired signal from the bottom, even at low levels.
The liquid surface can be reliably and precisely distinguished even at the very lowest levels, enabling the volume of the tank to be utilized more efficiently.
Conclusion
VEGAPULS 6X provides a dependable, contactless level measurement that can be simply isolated and retro-fitted. It requires minimal engineering and promotes optimized performance in LPG and LNG shipping, processing, and storage.
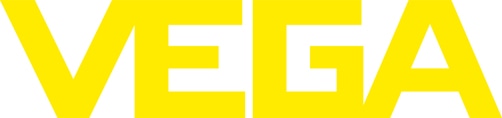
This information has been sourced, reviewed and adapted from materials provided by VEGA Grieshaber KG.
For more information on this source, please visit VEGA Grieshaber KG.