Security, mapping, and industrial automation are just some of the new applications for LiDAR systems. One sector garnering a lot of attention and development is the mobility market. LiDAR scanners are vital mechanisms in prototype systems for autonomous vehicles, as well as in systems used in adaptive cruise control (ACC), collision avoidance systems, traffic sign recognition, blind-spot detection, and lane departure warning. The “eyes” of the system, their sensors, are integral to their functioning; without them, none of these LiDAR systems can work.
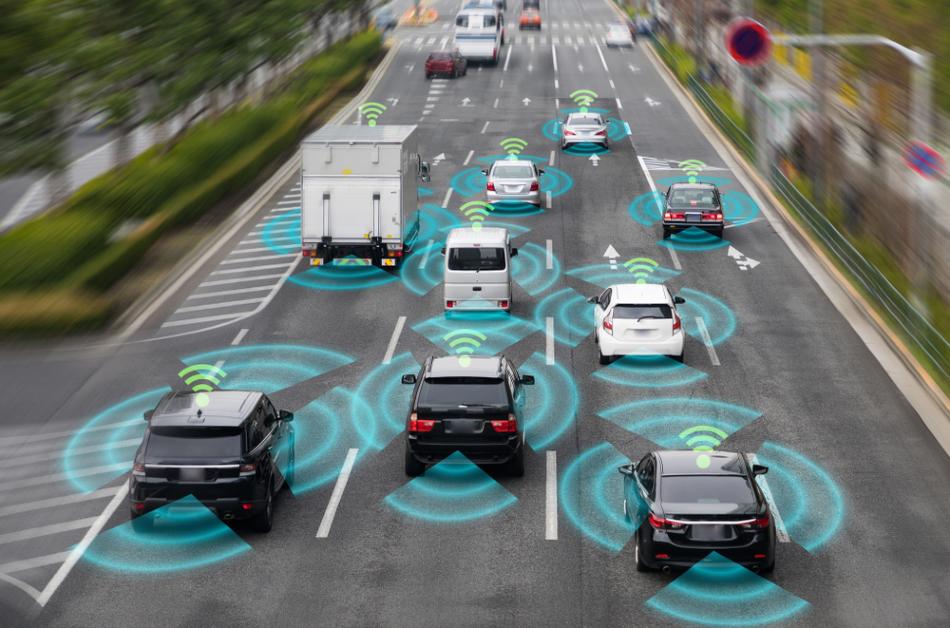
Image Credit: Shutterstock/metamorworks
This article will explore how design engineers for original equipment manufacturers (OEMs) of LiDAR systems can choose between the range of sensor technologies available.
Background
It’s crucial that mobility light detection and ranging (LiDAR) systems sense their immediate environment both quickly and reliably to create the best and most detailed picture of the surroundings and road ahead. For instance, systems mounted in fast-driving cars need to “see” up from 150 meters ahead, and sense objects of sizes as small as 10 cm in height.
.jpg)
Figure 1: LiDAR-scanner in action. Image Credit: First Sensor
Of course, this means the sensors have to cope with several technical challenges. The job requires complementary but independent sensor systems that are guaranteed function safely while also adhering to environmental standards.
For example, units should be rated for operating temperatures from -40 to 257 °F (-40 to 125 °C) to allow for environmental heating and heat generated from other system components. Sensors also have to have an optimum signal-to-noise ratio, in other words, to be able to detect signals through background noise. Additionally, optical detectors also have to be able to cope with varying levels of environmental light, meaning they must have wide dynamic ranges.
It’s important to note that the terms “detector” and “sensor” are sometimes used interchangeably, and the term “detector” may only refer to the photoelectric detecting element, while the “sensor” can include the detector and adjacent electronics providing functions like connectivity.
Basic economics also have to be considered by system designers when creating LiDAR systems, alongside the considerations of basic physics. Every component in the car should be as cost-efficient as possible. It’s often seen that for practical uses, the best cost to performance ratio is better than the best technology.
All current automotive mobility systems using long-range LiDAR are “scanning” devices that work by moving the laser beam step by step over an entire scene. Their effective range (with current technology) ranges from 30 to 300 m, and almost all of these long-range LiDAR systems are built around 905 nanometers (nm) lasers. These lasers emit invisible beams, are available at low cost in high volumes and use high power for short pulses (for example, 75 W peak for 5 nanoseconds). This presents an ideal power to cost ratio. These lasers have regularly found application with mature, low-cost silicon detector technology.
Selecting the Best Sensor Technology
Design engineers are applying a variety of different sensor technologies for LiDAR mobility systems as the industry makes progress, and their advantages and drawbacks are explored below.
Silicon PIN Diode Detectors
These silicon-based detectors feature a structure with layers of three semiconductor types: P-type, Intrinsic, and N-type. The detectors possess good dynamic range and can handle a wide range of light strengths. For example, they can detect the reflection of an object in the distance even when they are being exposed to direct sunlight. What’s more, these types of detectors are relatively cheap.
Their drawbacks lie in the fact that they are not able to deliver the high levels of bandwidth or signal-to-noise performance that the majority of modern mobility LiDAR systems need. Furthermore, they are not particularly sensitive or fast.
Silicon Photomulti Plier (SiPM) and Single-photon Avalanche Diode (SPAD) Detectors
These solid-state, silicon-based sensors were originally designed for small, specialized scientific and medical applications. More recently, designers have tried to find application for these detectors in the larger LiDAR market. Functioning similarly to avalanche photodiode detectors (APDs, discussed below), these sensors differ in that they are optimized for high internal amplification and gain, allowing them to be able to detect the smallest amounts of light.
Finally, they are very fast and are compatible with widely available CMOS technology, and therefore can be paired with associated electronics on the same chip. However, their single-photon counters are much less sensitive than APDs. As a result, they have to rely on very high multiplication.
Unfortunately, the multiplication process creates additional noise that substantially degrades the signal-to-noise ratio. Their amplification mechanism can also fall prey to false triggers brought on by high temperatures. The fact that the high gain of these sensors causes saturation problems could be considered their most significant drawback.
Firstly, these sensors have to cope with laser light reflected from objects ahead, and secondly, many LiDAR systems specify scanners with wide fields of view. This imposes a large amount of additional light on an SIPM or SPAD sensor. Some phenomena regularly seen in LiDAR mobility environments, from bright sunlight, high-beam headlights, to other LiDAR systems themselves, can saturate the sensor with more light than it is able to cope with, even with the use of optical filters.
As development in these sensors works to lessen their drawbacks, these sensors are often considered for many LiDAR applications. However, their problems with saturation, among others, have stopped them from becoming the detectors of choice for scanning long-range LiDAR.
.jpg)
Figure 2: Comparison of detection technologies. Image Credit: First Sensor
Indium Gallium Arsenide (InGaAs) Photodiode Detectors
These sensors are regularly used at small sizes in telecommunications glass fibers but are new to the range of LiDAR technology except for their use in specialized military or aerospace applications. This technology does not make use of conventional silicon-based construction for InGaAs material.
With specially built laser systems for its higher spectrum of 1550 nm, versus 905 nm for the other sensors discussed in this article, this design should possess higher sensitivity and be able to generate more power. Consequently, it can facilitate an automotive LiDAR system with a longer range than the majority of other sensors. However, a significant drawback is that the performance of an InGaAs’ detector can be substantially degraded by ambient temperatures that are only slightly above normal levels.
As a result, the sensor may require an external cooling system even in moderate climates. Furthermore, its base material is significantly more expensive than the silicon substrates that are popular in other designs. Fabricating InGaAs sensors in large sizes for use in LiDAR systems also need manufacturing processes that are far more complex than with silicon designs. Thus far, InGaAs sensors have not been successfully produced in high commercial volumes.
Finally, since this technology is new to the automotive LiDAR world, OEMs would need to spend a lot of time, effort, and revenue to develop a new LiDAR system based around an InGaAs detector.
Avalanche Photodiode (APD) Detectors
Originally fine-tuned for industrial and military applications, these silicon-based photodetectors function by allowing incoming photons to trigger a charge avalanche, multiplying gain by their internal amplification mechanism. Their structure, which is optimized for absorption, converts at least 80% of a laser’s reflected 905 nm light into photoelectric current. By doing this, APD detectors significantly increase their sensitivity.
Along with this optimal sensitivity, APDs possess an excellent signal-to-noise ratio, minimal saturation, and very good speed. Adding to their advantages is that they are also one of the cheapest sensor technologies available.
However, a drawback to these advantages is that APDs use specialized bipolar technology that may not be compatible with commonplace CMOS fabrication. As a result, they can only be sourced from a limited range of suppliers.
While they also can’t be paired on the same chip with their associated CMOS electronics, experienced suppliers can construct packages with sensors and electronics on closely adjacent chips. Both can be optimized for performances that exceed all others and this can be achieved without having to make compromises.
For example, an APD sensor array can be complemented by specially designed transimpedance amplifiers (TIAs) featuring customized gains and bandwidths to convert the photocurrent to voltage, and to condition the signal going into the system for high gain. This can capitalize on performance abilities, especially in low-light conditions.
APDs are manufactured by well-established, high-output commercial production processes, and their efficacy has been proven in a wide range of systems already on the road. When done correctly, APDs offer proven performance paired with a low cost. APDs are critical components in several of today’s most advanced mobility systems and are the go-to choice for long-range automotive LiDAR.
.jpg)
Image Credit: First Sensor
.jpg)
Image Credit: First Sensor
.jpg)
Figure 3: APDs. Image Credit: First Sensor
Selecting the Best Sensor Supplier
Once the right sensor technology has been chosen, LiDAR system designers still have to overcome the challenge of choosing the right sensor supplier, and all options have to be carefully assessed. Designers must consider whether the suppliers have the technology, capacity, and knowledge to adapt their sensors and systems to an OEM’s individual requirements and markets and whether they will work closely with the OEM team on design, manufacture, and scheduling to guarantee a winning time to market?
Insist on Experience
If a sensor vendor has to spend time on development, manufacturing, automotive qualifications, among other processes, the LiDAR mobility OEM will not benefit from a fast turnaround to market.
By doing the work, sensor suppliers gain valuable experience for OEMs. A good supplier will have already applied their sensor or detector technology for mobility applications, which could include both standard and customized APD design, standard and customized dyes, packages, and modules engineering and manufacture, along with the best electronics in the area. The perfect supplier will also boast a proven track record with products like automotive-grade APDs and associated electronics already being used by leading LiDAR OEMs.
Assess for Integrated Manufacturing
Designers should choose a supplier with appropriate technical benefits like sensors with the lowest noise and highest sensitivity. However, they should also choose a sensor supplier that upholds holistic control of its domain. The production process should be executed as a coherent whole from start to finish, from processing the chips to prefabricating the sensor systems.
By manufacturing all central components in-house, a supplier guarantees that all of their OEM products for series production and aftermarkets will be available long-term.
Check Customization Capabilities
To be successful as a manufacturer of LiDAR systems, it is vital to be able to realize the best cost to performance ratio. This can help a system stand out in an overcrowded market. Off-the-shelf sensors may not be suitable, and as such, components often have to be customized to fit a system design perfectly.
System makers should also find a sensor supplier that is flexible and responsive. Often, a supplier has to work with OEM designers to customize the sensor and its associated electronics to ensure seamless integration with the rest of the system, achieving optimal performance in the process.
For example, a team may need to establish sensor geometries that fit their choice of lenses or to optimize dimensions, or to adapt to the configurations of each unique optical design. A team may also need to determine the optimal channel count (how many signals are received in parallel) to exploit the scanner’s spatial resolution, while also customizing packaging for the shortest interfaces possible between a sensor and the electronics.
Finally, the best suppliers should also offer sensors with refined technical advantages such as multi-pixel homogeneity. This is because if photodiodes are not homogeneous or are obtained from a wide range of sources, they will not react in the same ways to ambient temperatures in real-world situations. This can significantly reduce the quality of performance in LiDAR scanners. Conversely, multi-pixel homogeneity can offer the tightest signal information distribution possible, even at peak distances.
Ask About Automotive Qualification
Another mark distinguishing a brilliant sensor supplier is that they already know the “rules of the road.” A supplier should be experienced in the most up to date automotive qualification, robustness validation, and characterization standards and regulations. Examples of this include:
- ISO/TS 16949 automotive-certified production and testing
- AEC-Q 102 and 104 automotive-qualified APD array packaging.
The supplier should also be able to apply these and other relevant standards to all of their components and manufacturing facilities to fulfill regulations and to aid system OEMs in avoiding liability.
Increasing regulation is inevitable in the manufacture of these systems, and good suppliers should be able to show demonstrated compliance with the regulation in documented best practices, like that seen in Ford Motor Company’s rigorous self-qualification for its Q Program.
Look for Future-proof Support
A great supplier should also demonstrate a proven track record of providing stellar quality and delivery performance along with high levels of support from the initial development stages right through to maintenance services.
Sensor design should be considered from the very beginning of the system design. If an OEM involves a sensor supplier early on, they will benefit from faster and easier design and manufacturing processes, which, in turn, results in LiDAR systems with enhanced performance capabilities.
Finally, a supplier should always be future-focused. By looking towards future developments in a very fast-changing field, they will possess a map of innovation, including expected regulatory, business, and technological developments they predict may arise in the future to help system makers navigate this ever-developing market.
Conclusion
The sensor is the eye of every LiDAR system. System designers have the option of choosing from a variety of competing sensor technologies, but many design engineers have come to believe that APD sensors offer the best combination of performance capabilities and monetary value.
LiDAR system makers should contemplate several aspects when choosing their preferred sensor supplier, from their experience and their ability to customize designs to their automotive qualification expertise. As LiDAR and other mobility technologies continue to develop, making the right sensor choices paves the way for the future.

This information has been sourced, reviewed and adapted from materials provided by First Sensor AG.
For more information on this source, please visit First Sensor AG.