Typically, taking measurements requires a balancing act between measurement range and precision. Pressure sensors are yet another piece of equipment that requires this delicate trade-off. It is important for researchers and product developers to decide, in any given pressure application, whether high-precision measurements are required at either the low-pressure end or the high-pressure end of the range.
When it comes to accurately measure pressures that vary over a large range, this can present some significant challenges. That is, until now. There’s a new flow-based differential pressure sensor, which is capable of making measurements across a ±5000 Pa range, with sub-pascal precision even at low-pressure regions.
With a huge breadth of application in multiple industries, pressure sensors can be used across the board – from medical equipment to leak detection. It has historically been difficult to measure pressures across a very wide range, despite the fact that there are many accurate ultra-low-pressure sensors available on the market today.
First Sensor has developed a new ‘breed’ of pressure sensor, which offers a way to measure these pressures across a wide range of values. Thanks to calorimetric flow-sensing technology, these high dynamic range sensors are now becoming possible. Firstly, it is important to explore how this technology works.
Using Calometric Principles to Measure Differential Pressure
This method of pressure sensing is one in which a differential pressure is measured with the flow of gas through the sensor, traveling from an area of high relative pressure to an area of low relative pressure. Known heat flux is supplied to the gas by an embedded heating element, and the flow rate of this is determined with two temperature sensors. The differential pressure can then be determined by measuring the flow rate.
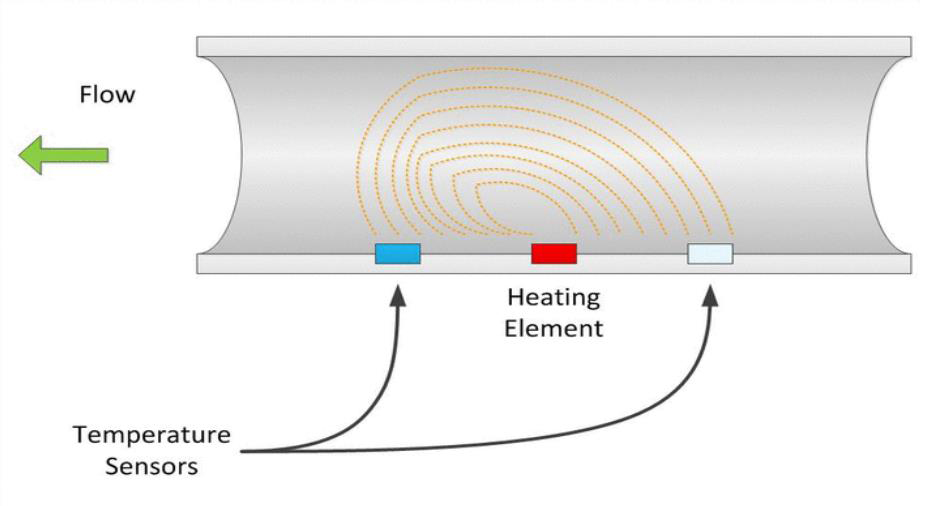
In their existing series of pressure sensors (LMI, LME, and LDE), First Sensor uses this calorimetry-based method, a few vital modifications.1,2
In these sensors, MEMS techniques are used to integrate microscale (60 μm) flow channel and thermal sensing elements together in a single silicon chip.
Against other, comparable sensors which use molded channels, this technique offers significant advantages. For instance, these smaller flow channels as produced by First Sensor facilitate high flow impedance, have an intrinsic immunity to issues of dust and humidity, and very low leakage rates.3,4
In narrow channels, extraneous factors like chimney effects and turbulence are non-existent, and gas behaves more predictably.5 This means that the result is a small, high-sensitivity, and robust pressure sensor.
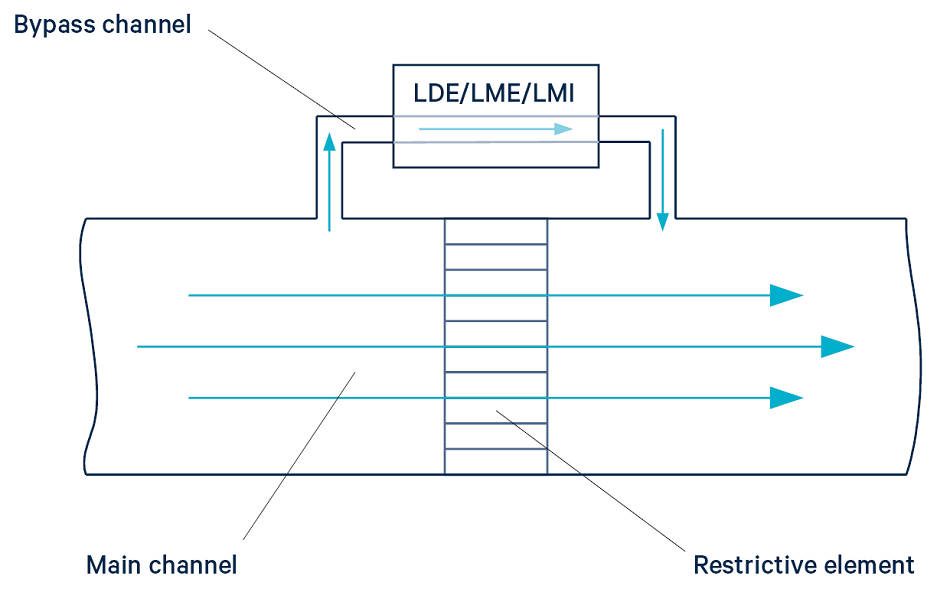
When measuring gas velocity or flow rate, it is advantageous to connect a sensor in a “bypass configuration”; in which high impedance of the sensor results in minimal interference with the main flow.6 The LDE/ LME and LMI sensor series is applicable to a huge range of applications thanks to their versatility and performance, including HVAC, medicine (respirators, anesthesia devices, etc.), and leakage measurement.
High Dynamic Range Measurement Problem
Measuring pressure variation with high accuracy remains an issue across a wide range, despite the high performance of these sensors. This is commonly described in terms of a system’s “dynamic range”. This term, dynamic range, refers to the ratio of the smallest value of some quantity (pressure, in this case) to the largest value. A ‘high dynamic range’ could accurately describe a system in which the flow rate or pressure varies hugely. However, generally, highly accurate pressure measurements can only be taken in a certain (and narrow) region, within that range.
In certain flow applications, this problem can be particularly prominent. As explored above, air velocity or flow rate measurements conventionally rely on the pressure measurements we described. However, generally, the functional elements of these flowmeters are nonlinear, and generated pressure can fluctuate approximately with the square of flow rate.
So, if the dynamic range of a given system is 1:100, then it follows that the pressure generated at the sensor has a dynamic range of approximately 1:10,000.
Historically, it has been difficult and problematic to accommodate this kind of dynamic range with a single accurate sensor device. That is, until now.
LHD ULTRA Series Pressure Sensors
The new range of LHD ULTRA pressure sensors from First Sensor expands on their existing calorimetric microflow technology, in order to deliver a versatile, highly-accurate pressure sensor which can provide precise and accurate measurements over a wide range.
With two microflow channels, LHD ULTRA pressure sensors also feature two sensing elements, on a single chip. One of these sensing elements has been designed to measure low differential pressures with high resolution, whilst the second sensing element has been designed to expand the measurement range over a region that is much wider. As a whole, the device facilitates accurate pressure measurements at low pressures, which have an extremely high dynamic range.
Signal processing is provided by an on-board microcontroller with accurate 24-bit analog-digital conversion.
This includes the stitching of the responses of the two elements, along with linearization, and temperature compensation. The resulting sensor is unparalleled in its precision, accuracy, and measurements.
The LHD ULTRA sensors from First Sensor provide pressure ranges which are between ±1250 and ±5000 Pa and have a resolution of around 50 mPa at low differential pressure values.
Each sensor provides the advantages in the performance of the existing pressure sensor ranges, LMI and LDE, including the immunity to humidity, dust and high flow impedance, and low leakage rates.
When using long tubing, no loss of sensitivity occurs, and these sensors offer truly unbeatable long-term precision and stability. This is because of First Sensor’s patented real-time offset compensation and linearization techniques, which both simplify obtaining pressure measurements and make them more accurate.
An on-board barometer is also featured within the LHD ULTRA to facilitate optional pressure output compensation, in addition to an operating compensated temperature range of -20 to +85 °C.
Learn more about the LHD ULTRA series here.
References and Further Reading
- LMI series-digital low differential pressure sensors. Available at: www.first-sensor.com.
- LDE series-digital low differential pressure sensors. Available at: www.first-sensor.com.
- LDE/LME/LMI Series-superior immunity to humidity. Available at: www.first-sensor.com.
- LDE/LME/LMI Series-dust test. Available at: www.first-sensor.com. (Accessed: 28th April 2020)
- Whitesides, G. M. The origins and the future of microfluidics. Nature 442, 368–373 (2006).
- LDE/LME/LMI pressure sensors in bypass configuration for gas flowmeters. Available at: www.first-sensor.com.

This information has been sourced, reviewed and adapted from materials provided by First Sensor AG.
For more information on this source, please visit First Sensor AG.