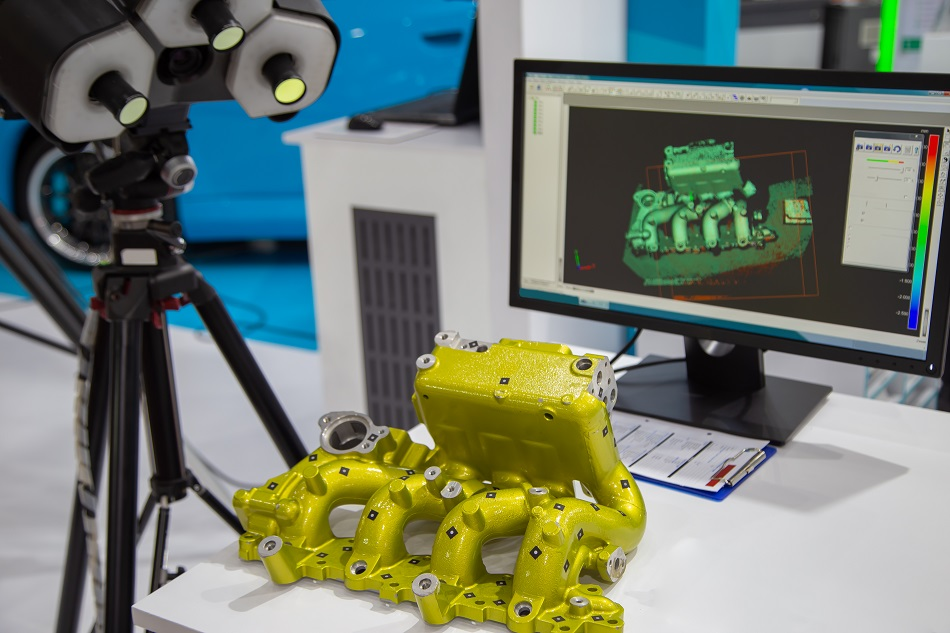
Image Credit: Itsanan/Shutterstock.com
The rapid growth and continuously advancing field of sensor technologies has supported the widespread application of three-dimensional (3D) imaging technology, particularly within the industrial setting.
3D Imaging Sensors
The development of three-dimensional (3D) imaging technology was originally inspired by the interest of researchers to create highly sophisticated image processing systems capable of obtaining images that closely resemble that which can be perceived by the human eye. As sensor technology has advanced over the past several decades, 3D imaging sensors have found their usefulness in several different applications ranging from biomedical image analysis, robot guidance and autonomous navigation to oceanography, microscopy, astronomy, and virtual reality.
Industrial Applications
Within both the mechanical and manufacturing industries, 3D imaging sensors are used for surface quality control, as well as both micro- and macroprofiling. Traditionally, both optical and contact probes were used together to not only maintain quality control but also measure the accuracy and efficiency of the industrial process through a contactless and optical method.
While optical and contact probes remain useful for these purposes, 3D imaging sensors have dramatically changed the way in which data is collected. For example, Coordinate Measuring Machines (CMMs), which provide precise measurements of objects for a wide range of industrial purposes, typically require both 3D measurement sensors and contact probes to be incorporated into their system. Similarly, many collision avoidance systems and robotic applications, which previously relied on two-dimensional (2D) vision sensors for data collection, have instead turned to 3D imaging and range sensors.
In addition to the aforementioned applications, 3D imaging sensors used within the industry also provide data on the dimensions, roughness, waviness and form factor of products. Additionally,
3D Scanning
Since its introduction into the market, 3D imaging and scanning devices have primarily been used to ensure quality control and continuous inspection of robotics and machine vision systems. As this technology has become more accessible to other industries, the 3D laser scanning market has skyrocketed to a value of approximately $3 billion USD in 2016. In fact, researchers have estimated that the growing use of laser scanning will bring this market to a value of $10 billion by the year 2024.
Following the construction and architecture industries, topographic mapping accounts for approximately 44% of the global demand for 3D imaging sensors. In the industrial field, single-point laser triangulation lasers are most commonly used to assess distances, diameters, and thickness, in addition to maintaining surface quality control. Single-point laser triangulators, which function according to the active triangulation principle, are well-known for their precision and accuracy capabilities, as well as their relative sensitivity to unusual surface textures or illumination conditions.
Advancing 3D Mapping
The use of 3D mapping technology has become commonplace in a wide range of industries for surveying and material monitoring. In addition, 3D mapping technology has been used to study human anatomy, create 3D recreations of the stars, planets, and galaxies and assist engineers in design development.
In a recent Sensors publication, researchers discuss a novel 3D Simultaneous Localization and Mapping (SLAM) technique that has improved sonar mapping and even allowed for swath profiles of the seafloor to be generated. Although the SLAM system has been traditionally used on land for mobile robotic purposes, its application for underwater studies has provided rapid refresh rates and greater resolution images as compared to those achieved by traditional sonar sensors.
Sources and Further Reading
- Otesteanu, M., Gui, V. (2008). 3D Image Sensors, an Overview. WSEAS Transactions on Electronics 3(5);
- “Coordinate Measuring Machines (CMM) Information” – Engineer ing 360
- “2019 3D Trends Study: 3D Imaging Market Growing, Including Geospatial” – Point of Beginning Online
- Sansoni, G., Trebeschi, M., & Docchio, F. (2009). State-of-The-Art and Applications of 3D Imaging Sensors in Industry, Cultural Heritage, Medicine, and Criminal Investigation. Sensors 9; 568-601. DOI: 10.3390/s90100568.
- Palomer, A., Ridao, P., & Ribas, D. (2016). Multibeam 3D Underwater SLAM with Probabilistic Registration. Sensors 16(4); 560. DOI: 10.3390/s16040560.
Disclaimer: The views expressed here are those of the author expressed in their private capacity and do not necessarily represent the views of AZoM.com Limited T/A AZoNetwork the owner and operator of this website. This disclaimer forms part of the Terms and conditions of use of this website.