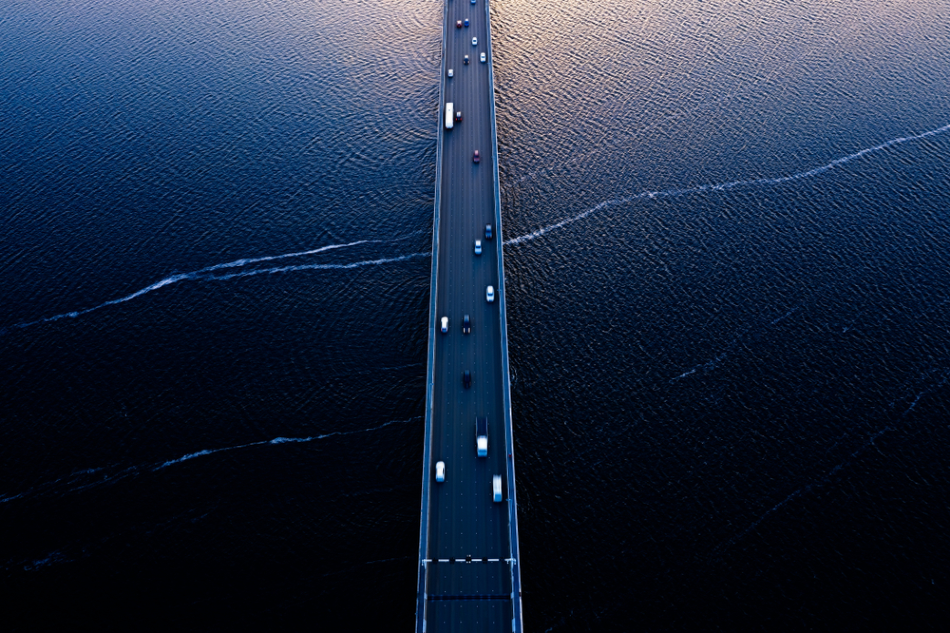
Image Credit: Andrew Atkinson/Shutterstock.com
Toshiba has introduced the use of a Sensor-Based Structural Health Monitoring (SHM) system to fight aging infrastructure.
In the upcoming fourth industrial revolution, technologies such as SHM are believed to have significant contributions in shaping the ways to respond against adverse structural changes, improving structural reliability and life cycle management.
Structural Health Monitoring: Why Use It?
The global investment in infrastructure is currently growing at a rapid rate. Two primary factors fuel this boom:
- The aging of the infrastructure in the developed world
- Economic growth, especially in the developing world
Most of the existing infrastructure across the world is in a stage that demands extensive maintenance and management. However, the human resources needed for such maintenance can be huge. This is where structural health assessment or SHM comes to play. It is an important tool to get an idea of the location and extent of damage in any aging infrastructure in an automated way and can help in minimizing maintenance costs and extend service life.
Applications of SHM Across Other Sectors
Other important applications of SHM are in the aerospace sector, the manufacturing of wind turbine systems, civil engineering, architecture, mechanical, and marine systems. Carefully applied SHM can help determine the real-time health performance of an aircraft.
Whether the structure will survive based on damage severity is a very important aspect of aircraft maintenance/manufacturing. Other factors that can be monitored using SHM are dynamic strain, damage due to impact, loads on wings, detection of cracks and deformation, composite landing gears, and pressure value in the hydraulics system.
In the case of wind turbine systems, SHM helps designers to design rotors with reduced weight and can replace conservative design ideas with careful and precise automation. Information about loads and the damage arising from these loads might help manufacturers to improve the wind turbine designs and manufacturing and subsequent quality control processes.
Different SHM Techniques: Passive and Active Responses
SHM can be based on passive and active responses. Passive involves condition monitoring, where the periodic response received is compared with the available data to detect any abnormal effects in signal which may have its source from changes in the structural integrity.
On the other hand, monitoring the signal and giving feedback to the system with respect to changes in signal is an active response. The extraction of the features that potentially gives the idea of structural damages from these measurements and the subsequent statistical analysis of these features helps to determine the current health state of the structure concerned.
Even though it has been found that vibration-based inspection methods are better than non-destructive testing (NDT) methods for SHM, they are not fully developed. Therefore, they need to be used in conjunction with various NDT to fully understand the health of a structure.
Acoustic emission (AE), ultrasonic, fiber optic, laser Doppler vibrometer, and thermal imaging are some of the methods used in SHM for damage detection. Toshiba’s brand-new sensor-based structural monitoring system exploits the concept of elastic waves emitted by defects in a structure that is perturbed by an external source.
For example, when a heavy vehicle crosses a bridge with structure defects, the new sensor-based technology converts the elastic waves emitted by the damaged area in the bridge to visualized data. The sensor collects data from the portion of the bridge where it is attached using the AE method.
Table 1: A representation of the advantages and disadvantages of various NDT methods as mentioned by Rytter. A (+) symbol indicates only a partial applicability of a method to the actual purpose. Source: Rytter, A/University of Aalborg.
|
1
|
2
|
3
|
4
|
5
|
6
|
7
|
8
|
9
|
Visual Inspection
|
+
|
(+)
|
-
|
-
|
(+)
|
-
|
+
|
+
|
(+)
|
Vibration Inspection
|
+
|
+
|
-
|
-
|
+
|
(+)
|
+
|
+
|
(+)
|
Acoustic Emission
|
+
|
+
|
-
|
-
|
+
|
(+)
|
+
|
+
|
-
|
Ultrasonic Testing
|
-
|
-
|
+
|
-
|
+
|
-
|
+
|
+
|
+
|
Magnetic Particle
|
-
|
-
|
+
|
-
|
-
|
-
|
+
|
+
|
(+)
|
Radiography Testing
|
-
|
(+)
|
+
|
-
|
+
|
-
|
-
|
+
|
+
|
Eddy Current Testing
|
-
|
(+)
|
+
|
-
|
-
|
-
|
+
|
+
|
(+)
|
1: Usable for Global Inspection
2: No cleaning required
3: Not sensible to measurement noise
4: Stand alone
5: Detection of internal defects
6: Detection of defects far away from sensors
7: Defects in areas with one surface accessible
8: Defects in areas with two surfaces accessible
9: Estimation of the size and location of the defect
As stated in the table above, acoustic emission is one of the most promising methods that can be developed to cover all nine purposes.
Acoustic Emission: How Does it Work?
Acoustic emission is the emission of acoustic/elastic waves from solids when there are internal structural changes happening in the materials, including crack formation or plastic deformation due to aging, temperature change gradient or external mechanical forces.
Several local sources of elastic waves are created due to these structural changes, which, in turn, results in small surface displacements in a material. In this way, the accumulated elastic energy in a material is released. In structural health monitoring, AE is used to detect the type and location of the internal damage.
The AE non-destructive tests are performed by sensors characterized by the following features:
- The sensors have high sensitivity and imperfection analysis can be precisely examined
- The sensors differentiate between developing and stagnant defects
- Where the sensors are attached, specimens do not need to be thoroughly processed
SHM Sensors Found Detecting Damage Using Guerrilla Rainstorm
The AE non-destructive testing of materials is typically significant for elastic waves within a range of 100 kHz and 1 MHz. However, the sensors developed by Toshiba for its SHM system can even detect elastic waves emitted by raindrops that usually lie in a range of 2~50 kHz.
Despite the fact that the systems that use AE generally classify waves generated by raindrops as noise and avoid usage of data from such source, Toshiba’s sensors were able to detect the elastic waves generated due to the impact of raindrops.
Click here for more information on sensors technology.
They calculated the distribution of the raindrops and used this to predict the location of cracks in the interior of the structure as stated by Kazuo Watabe, who is the chief research scientist at the Mechanical Systems Laboratory at Toshiba’s R&D Center.
The usage of raindrops as a source of elastic waves would decrease the overall data collection time for the sensing process of damage detection and location. This has opened up the possibility to explore a previously untested domain of sensor technology using AE, where during heavy rain, every raindrop could be used to sense deterioration, even in areas with reduced traffic flow.
【TOSHIBA】Structural Health Monitoring
Video Credit: Toshiba News and Highlights/YouTube.com
Future Work
Takashi Usui, a Research Scientist at Toshiba has mentioned the possibility of extending the concept of using raindrops distribution in SHM to monitor other social infrastructures such as roads, buildings, and even large-scale industrial machinery in the near future.
However, before increasing the scalability of this technology in other structural maintenance and improvement, considerable work still needs to be performed for verification tests through the collection and analysis of data. This will help to improve the overall reliability of the system.
Increasing the future accessibility of this kind of technology in SHM across all sectors will ensure perfect automation at a lower cost and ensure the safety of our infrastructure and society.
References and Further Reading
Hamdan, A., Sultan, M.T.H., Mustapha, F., ‘Structural health monitoring of biocomposites, fibre-reinforced composites, and hybrid composite’. Woodhead Publishing Series in Composites Science and Engineering (2019) Pages 227-242
‘An Aging Population, an Aging Infrastructure: How Structural Health Monitoring Combats Both of These Social Issues’, Mechanical Systems Laboratory, Corporate Research & Development Center, Toshiba Corporation. Available from: https://www.toshiba-clip.com/en/detail/7219
Mukhopadhyay S.C., Ihara I. Sensors and Technologies for Structural Health Monitoring: A Review. (2011) Lecture Notes in Electrical Engineering, vol 96. Springer, Berlin, Heidelberg
Nystuen J.A., ‘Listening to Raindrops from Underwater: An Acoustic Disdrometer’ (2001) J. Atmos. Ocean. Technol.
Rytter A., ‘Vibration based inspection of Civil engineering structures.’ University of Aalborg (1993)
Disclaimer: The views expressed here are those of the author expressed in their private capacity and do not necessarily represent the views of AZoM.com Limited T/A AZoNetwork the owner and operator of this website. This disclaimer forms part of the Terms and conditions of use of this website.