The FrieslandCampina Group firm Kievit, based in the Netherlands, is an expert in creating flavor sensations.
It is the quality of the ingredients that guarantees a delectable taste, smooth texture, and sensory excellence in food and beverages.
Together with our customers, we develop ingredients for the food and beverage industry, such as foaming cream agents, coffee and cocoa blends, fat powders, whipping agents, functional blends, micro-encapsulation, and cake emulsifiers.
Ger van den Ber, Director, BergTopadvies B.V.
Emulsification, spray drying, microencapsulation, and agglomeration are a few of the technologies used to turn liquids into powders or give products certain qualities.
Long-Term Partnership
For almost 15 years, FrieslandCampina Kievit has relied on sensors from Schiltach for pressure and level measurement. Over time, a wide range of VEGA sensors have been deployed across the facility.
van der Ber added, “I appreciate the reliability of the instruments and know that there’s no need to worry about them. Over the years, you simply get a feeling for whether an instrument works well or not.”
Since 2006, a radar sensor from VEGA has been taking measurements in the raw material silo. Only the 26-GHz VEGAPULS 68 was offered at the time. Since this specific raw material’s Dk value is so low, reliable measurement has always been difficult.
The technical team swiftly shifted to the instrument with the higher frequency when VEGAPULS 69 with 80-GHz technology was introduced to the market. Therefore, all of the prior measurement uncertainties were removed at once.
A VEGAPULS 61 non-contact radar level sensor in wastewater treatment, along with the point level switches VEGACAP, VEGASWING, and VEGAVIB in a variety of applications, have all been in operation since 2011.
Various industrial processes, such as the storage of fats and filter monitoring, are also being observed by many pressure-measuring devices from VEGA.
Prompt Intervention
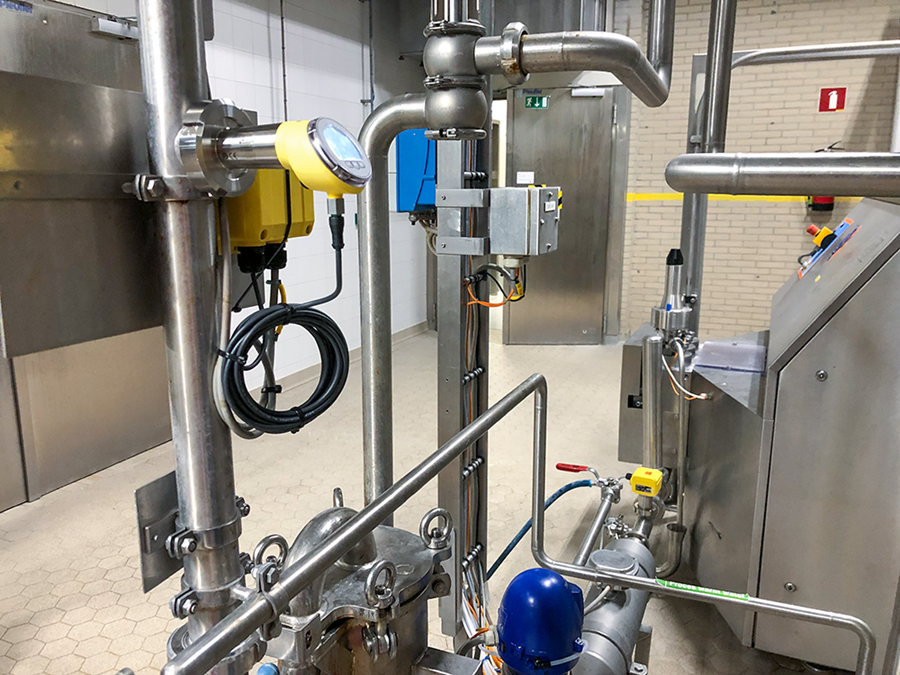
Image Credit: VEGA Grieshaber KG
However, one measurement point has been under close scrutiny for many years: the location where emulsification is observed. There, the process conditions are typical for the manufacturing of food. It is heated, the process water is 85 °C, and pressure surges and powerful vibrations are frequent occurrences. The pressure in the pipes typically ranges from –1 to +8 bar.
When the emulsion reaches a specific temperature, a high-pressure pump is applied. This circulatory system must maintain continuous pressure to feed the high-pressure pump. Therefore, a pressure meter was put downstream of the pump to find filter contamination early on.
van den Berg further stated, “In the past, pressure gauges from another manufacturer were used here, but due to their short lifespan they always caused problems.”
Other measurement concepts, including flow measurement, also had problems. On the one hand, moisture intrusion led to issues, while on the other, the diaphragms of the sensors frequently failed.
“However, this measurement is absolutely necessary for the overall process, as it is the only way to monitor the contamination of the filter, which in turn is crucial for the proper functioning of the pump,” van den Berg noted.
Even before its formal market debut in August 2019, the new VEGABAR 38 was already installed at this measuring point. It is a pressure transmitter with a ceramic measuring cell that is globally applicable and can measure gases, vapors, and liquids up to 130 °C.
This incredibly small sensor makes simple and extremely effective automation possible. Above all, there are no concessions made in terms of cleanliness, safety, or accuracy—exactly the conditions that are essential in the manufacturing of food.
A Plus in Operational Safety
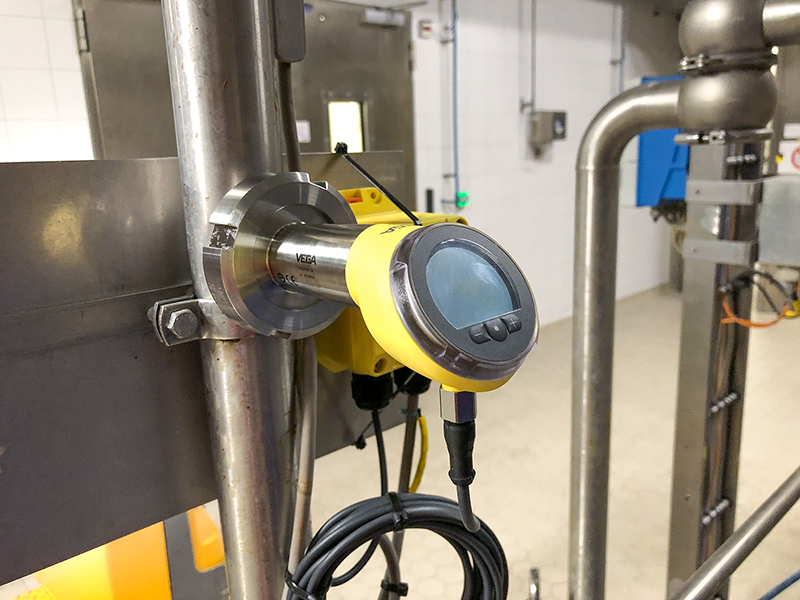
Image Credit: VEGA Grieshaber KG
Installing the new sensor series is easier due to its universal connection for hygienic adapters. Process fittings can be chosen and modified according to the on-site requirements. The sensor features a display with on-site tuning options in addition to a full-color 360° status display that serves as a distinctive highlight.
This is not just for aesthetic reasons; because the hue of the lit ring can be freely chosen, it can also be adjusted to poor lighting. The user can quickly determine if the sensor is switching, if the measurement process is active, or if there is a problem with the procedure.
The IO-Link standard protocol guarantees both ubiquitous and straightforward communication. As a result, the instruments feature a defined communication platform that enables easy system integration and smooth data transfer.
A smartphone or tablet can simply read out and set the new VEGABAR measuring instrument line. This method significantly simplifies sensor setup and operation, especially in situations with several pipelines and connected production processes where access is challenging and time-consuming. In his regular job routine, van den Berg highly values this aspect.
Simple, Reliable Setup and Commissioning
🚦 How do sensors with a colour status display provide more visibility to a process? | VEGA talk
Video Credit: VEGA Grieshaber KG
Since this initial deployment was essentially a pilot run, the VEGA crew was present during the installation.
van den Berg further added, “In the future, however, we will handle everything ourselves. Thanks to Bluetooth being compatible with the app or PACTware software, the setup and monitoring of the VEGA instruments is very easy.”
He had long since come to value the excellence and dependability of VEGA devices and VEGA service.
He also noted, “I like the color. After all, it is also nice to have equipment that looks great.”
He noted that the pressure sensors had been operating flawlessly since they were installed.
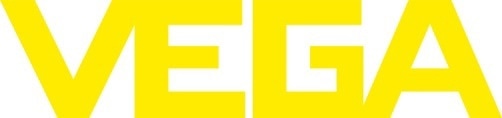
This information has been sourced, reviewed and adapted from materials provided by VEGA Grieshaber KG.
For more information on this source, please visit VEGA Grieshaber KG.