Laser triangulation sensors determine the position of a target by measuring the reflected light from the target surface. Based on their intended application and performance, these sensors can be classified into two categories. High resolution lasers are generally utilized in position and displacement monitoring applications that require stability, high precision and low temperature drift.
Proximity type laser triangulation sensors are often employed to detect the presence of a component, or utilized in counting applications. They are also less expensive when compared to other high performance technologies. This article describes the properties of high resolution solutions, their advantages and disadvantages, operating principle, and applications.
Operating Principle
Laser triangulation sensors include a CMOS/CCD or PSD detector and a solid-state laser light source. They operate on the basic principle wherein a laser beam is projected on the target under measurement and a part of this beam is then reflected via focusing optics onto a detector. As and when the target shifts, the laser beam moves on the detector (Figure 1).
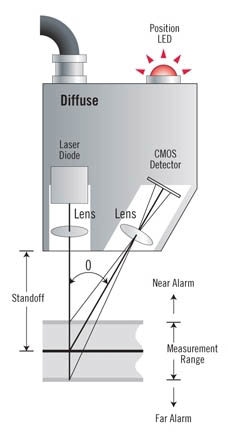
Figure 1. Laser triangulation principle
The detector sends a signal which is utilized to measure the relative distance to the object or target. This data is usually available through a digital (binary) interface, an analog output, or a digital display for processing.
PSD type sensors can determine the beam centroid depending upon the whole reflected spot on an array, while CCD and CMOS type sensors are capable of detecting the peak distribution of the quantity of light on a sensor pixel array to find the target position. Therefore, PSD type sensors are highly sensitive to fake reflections from variable surface conditions and this in turn reduces their precision. However, these sensors provide excellent resolution when quantifying specular targets or ideal matte finishes.
CCD and CMOS type sensors are more precise across a broader range of surfaces. This is because position is typically determined using maximum charged pixels from the reflected beam. Pixels with lower charge are generally energized by unnecessary reflections from variable optical properties of the surface under measurement and can be overlooked during signal processing.
This enables lower charged pixels to be deployed in a wide range of applications. Signal distribution variation between PSD and CMOS is shown in Figure 2. This emphasizes the potential precision problem related to PSD type sensors.
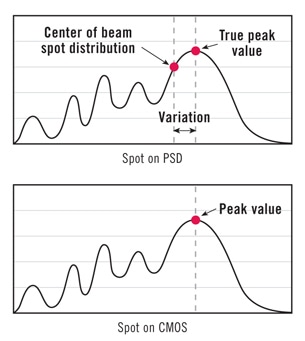
Figure 2. Potential errors induced by PSD type laser sensor
Additionally, laser triangulation systems can also be utilized on surfaces that are highly reflective. This is commonly dubbed as specular surfaces. However, standard triangulation sensor cannot be used on these surfaces because the laser light would reflect back into itself. In such cases, the beam should be directed at the object or target at an angle. This beam will bounce from the object at an equal but reverse angle and then center onto the detector.
MTI Instruments offers laser heads that are particular designed for specular surfaces. The company’s lasers can be strategically placed at an angle and used in the specular mode if required. The working principle of a specular laser head is shown in Figure 3.
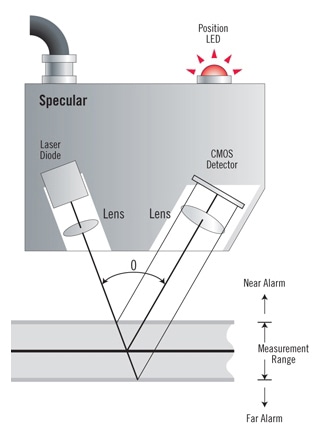
Figure 3. Specular laser triangulation principle
Characteristics of Laser Sensors
Range/Standoff Distance
Laser triangulation sensors have an ideal operating point, also known as the standoff distance. At this operating point, the reflected spot is in the middle of the detector and the laser is found at its sharpest focal point. A sensor’s optical design determines its range and standoff distance. Figure 4 shows a diagram that envisages the variation between two types of acceptance angle sensors.
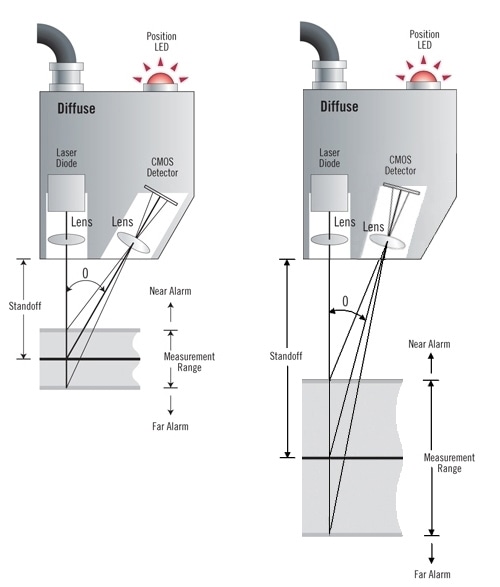
Figure 4. Laser acceptance angle dictates the sensitivity and measurement range
Non Contact
Laser displacement sensors are non contact by nature, which means they can accurately measure the displacement or position of an object sans touching it.
Sensitivity
In the context of measurement solutions, sensitivity is defined as the ratio of displacement that occurs per unit of measurement, and is usually expressed in microns/milli-volt. In majority of cases, high sensitivity results in greater resolution. The output of two sensors with different sensitivities is illustrated in Figure 5.

Figure 5. Sensitivity is determined by the slope of the sensor output response
Resolution
When laser triangulation sensors are properly designed, they provide excellent stability and resolution. Resolution as such refers to the smallest amount of distance change which can be easily determined. The main factor used for ascertaining resolution is the electrical noise of the system.
Spatial Resolution
During measurements, laser sensors offer a distance that is roughly equivalent to the typical surface location within the laser spot. Although these systems cannot precisely detect the position of features, they can repeatably measure uneven surfaces. Therefore, the laser spot must be 25% smaller than the feature being measured.
Bandwidth
The cutoff frequency or bandwidth of a system is described as the point where the output is decreased by -3dB. This is roughly the same to an output voltage drop of 30% of the exact value.
Linearity
In a suitable condition, the sensor’s output would be completely linear and would not diverge from a straight line at any situation. However, there will be small deviations from this line which define the linearity of the system. Linearity is generally denoted as a percentage of the Full Scale Measurement Range (FSR).
Advantages and Disadvantages
One major advantage of laser sensors is that they can resolve measurements less than one micron at reduced cost when compared to other technologies. Their measurement range is also large, which enables them to meet a wide range of application requirements. Thanks to the large operating distance, there is adequate standoff to cut down potential damage from contacting the shifting object.
However, it is important to ensure that laser systems are clean and free from dirt and other foreign materials, otherwise accuracy will be affected. Since laser heads have electronic components that are highly sensitive, their operating temperature is somewhat restricted. Also, vacuum installations cannot be carried out sans external cooling.
Applications
Laser triangulation sensors are used in the following applications:
- Position Sensing: Robot location, railroad track alignment, pavement and concrete road profiling, and welding head position
- Dynamic measurements: Piezoelectric characterization, spindle runout analysis, in-line process monitoring, and ultrasonic vibration measurements
- Thickness and dimensional measurements: Quality control during concrete block manufacturing, process monitoring of wood thickness, brake rotor thickness, and separation distance between rollers
Conclusion
Laser triangulation sensors are high resolution systems that are often employed in position and displacement monitoring applications where low temperature drift, excellent stability, and high precision are required.
About MTI Instruments
MTI Instruments is a worldwide leader in the design, manufacture and engineering of non-contact measurement systems and sensors.
MTII’s main products consist of computerized general gauging instruments for position, displacement, thickness and vibration applications based on laser triangulation, fiber-optic and capacitance measurement technologies.
The Semiconductor Products sensor group manufactures manual, semi-automated and fully automated wafer characterization tools designed to measure wafer thickness, total thickness variation (TTV), bow, warp and flatness of semi-insulating and semiconducting materials.
MTII’s Aviation Balancing Instruments group provides state-of-the-art portable balancing and vibration analysis systems for turboprop and jet aircraft engines.
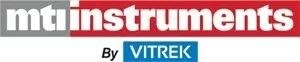
This information has been sourced, reviewed and adapted from materials provided by MTI Instruments.
For more information on this source, please visit MTI Instruments.