Mar 18 2016
Subsea 7 LLC., a leading global contractor in seabed-to-surface engineering, construction and services, and 3D at Depth, a global technology provider of advanced subsea LiDAR systems and solutions, have announced the completion of several metrology projects using subsea LiDAR technology in new configurations to help increase overall efficiencies in offshore oil and gas applications.
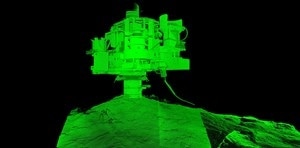
To meet the complex requirements for the metrologies and to reduce time, Fred Goodloe III, Project Surveyor Subsea 7 worked closely with 3D at Depth's Mark Hardy and Derek Perce to determine the optimum solution to complete the scope. Subsea 7's Gulf of Mexico project is considered to be the world's first in tandem metrology, deploying LiDAR sensor technology on dual remotely operated vehicles (ROVs) for simultaneous scans. The project shortened overall survey project schedules and reduced timeline to first oil.
Subsea 7's project stationed two 3D at Depth SL1 systems independently to collect simultaneous metrologies utilizing separate ROVs. The survey conducted in the Mississippi Basin completed a total of six spool metrologies. The on-bottom data collection time for both metrologies was 2.5 hours. Data was then processed on board and issued 5 hours post-metrology completion, a measurable reduction in accessing actionable data. The ranges achieved by 3D at Depth's sensor technology allowed for a single set up and scan over a 220°-degree arc, collecting repeatable measurement data with a transmit and receiving beam steerable to the areas of interest. This flexibility allowed a high collection density without the need for multiple set up and scan locations, the placement of additional frames or tripods for registration spheres, and other acoustic ranging devices. Throughout the process, the project timeline included a best practice method by collecting dual independent scans on each spool metrology, which offered 100% data redundancy. Conventional long baseline positioning (LBL) methods would have required longer timeframes in terms of configuration and data set delivery schedules. The in tandem configuration, along with onsite topside access to data, resulted in significant cost savings in terms of vessel time and schedule, and facilitated a reduced time to first oil.
"Successful implementations, substantiate the flexibility of LiDAR scanning technology for broader use in the offshore industry," said 3D at Depth Subsea LiDAR Specialist, Derek Perce. "3D at Depth will continue to provide our customers with innovations to LiDAR technology that demonstrate performance and increase the efficiencies of data collection, mapping and visualization."
3D at Depth recently made the news with their announcement on completing the 107th metrology: 3D at Depth Metrology News.