Process engineers at oil/gas refineries will find the rugged ST100 Thermal Mass Flow Meter Series from Fluid Components International (FCI) provides highly accurate, dependable measurement of air and fuel gases to optimize the performance of the boilers utilized by sulfur recovery units (SRUs).
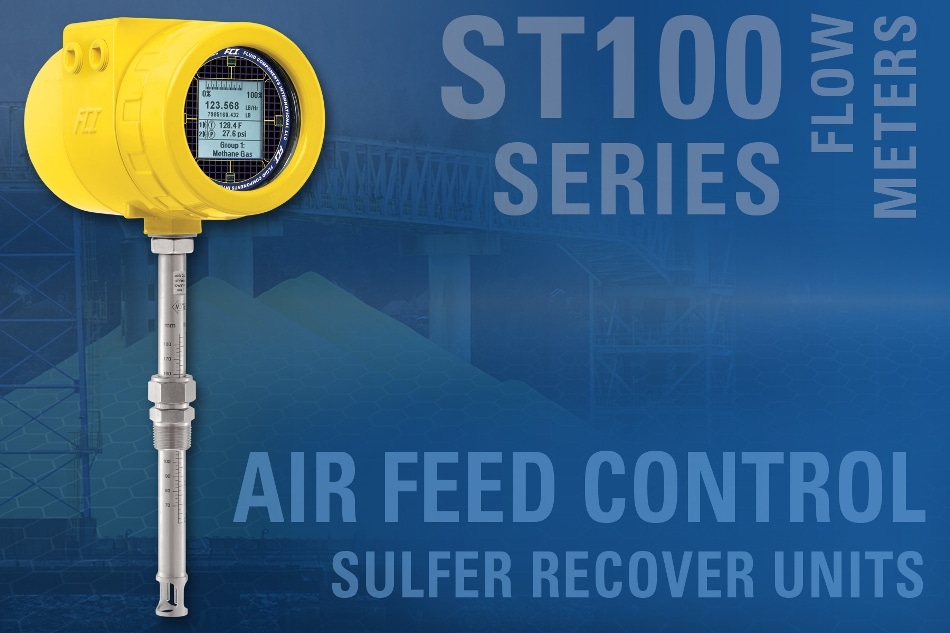
Hazardous toxic levels of sulfur are present in various forms during the production and refining of hydrocarbon fuels (crude oil), including sulfur dioxide (SO2) gas and hydrogen sulfide gas (H2S). The sulfur found in crude oil products is toxic and presents a serious hazard to workers, equipment and facilities and must be removed during the production process.
The typical SRU Claus sulfur removal process operation consists of a burner system for the combustion of the sulfur rich sour gas (“acid gas”) followed by a catalytic converter to produce outputs of harmless sulfur powder, water and waste gas (“tail gas”). Tail gas from the SRU can be further treated by either a flue gas desulfurization (FGD) or a thermal oxidizer.
The operation of SRUs requires closely controlling the ratio between the H2S acid gas, the tail gas and the available oxygen (air) as crucial to effective operation of the system. The SRU system’s air feed includes a main air feed and a trim air feed to closely control the total air feed to the boiler. Closely monitoring air flow is essential at multiple points in the process.
FCI’s ST100 Meter is ideal for air feed control measurement in this process. Featuring a thermal dispersion technology flow sensor design, the ST100 meter combines repeatable measurement with feature- and function-rich electronics. It provides direct gas mass flow measurement and requires no additional sensors or flow calculating devices. The instrument’s no-moving parts design also virtually eliminates wear, breakage and maintenance.
The basic insertion-style ST100 Flow Meter measures air/gas flow from 0.25 to 1000 SFPS (0.07 NMPS to 305 NMPS) with accuracy of ±0.75 percent of reading, ±0.5 percent of full scale. A wide variety of pressure ranges can be specified from 0 to 1000 psig [0 to 70 bar (g)], depending on the specific model selected to support the most demanding applications.
When selecting the ST100 Meter, users have multiple communication options. They can choose from: 4-20 mA analog, frequency/pulse, or certified digital bus communications such as HART, Foundation Fieldbus, Profibus PA or Modbus RS485. Should a production field or plant’s communication needs change, a new replaceable card can be swapped out in the field.
Developed with a graphical, multivariable backlit LCD display, the ST100 meter brings new meaning to the term “process information”. Its sophisticated readout continuously displays all process measurements and alarm status for easy on-site viewing by technicians, and it has the ability to query for service diagnostics.
The ST100 meter’s electronics include a user selectable and programmable data logger. Readings are stored in a removable, internal micro-SD card. The micro-SD card has a 2 GB capacity capable of storing approximately 21 million readings. The recording time base is user selectable with a maximum rate of 1 reading per second. The logging feature is selectable via the front panel menu or via the serial port and configuration software tools.
The ST100 meter utilizes constant power thermal mass flow sensing technology that measures flow with 100:1 turndowns in ranges from 0.006 to 1850 SCFM [0.01 to 3140 NCMH]. The transmitter/electronics are integrally mounted with the flow body or can be remote mounted to 1000 feet [305m] away. The transmitter enclosure is NEMA4X/IP67 rated and available in painted aluminum or stainless steel.
ST100 meters are agency approved for hazardous environment installations. FCI products undergo rigorous agency testing and obtain their approvals on the entire instrument, not just the enclosure. Approvals available for the SIL rated ST100 Flow Meter include: FM, FMc, ATEX, IECEx, EAC/TRCU, CPA, NEPSI, InMetro, and CE Approved.
Fluid Components International is a global company committed to meeting the needs of its customers through innovative solutions for the most challenging requirements for sensing, and measuring flow, pressure and temperature of gases.