Viatran pressure transmitters are developed using four types of pressure sensors. This is in response to field research which yields data regarding the actual requirements of different applications, following which appropriate technologies are incorporated into the solution for each issue. The four types of sensors used in pressure sensors are ceramic piezoresistive, bonded foil strain gage, silicon piezoresistive, and variable capacitance. Among these, no single type is ideal for all kinds of pressure sensing applications, but there will be one or more that are ideal for any given situation. An overview of the benefits and disadvantages of each type is given below.
Bonded Foil Strain Gage Sensors
The principle of bonded foil strain gage pressure sensing technology is the Wheatstone Bridge, an electrical circuit with four branches, each having equal resistors. In accordance with this balanced circuit, four metal foil strain gages are bonded to a metal diaphragm, each bond acting as one of the four circuit branches and providing the function of variable resistors in the circuit, as shown in the following diagram. When no pressure is applied (zero), the diaphragm is undeflected and the Wheatstone Bridge is balanced, resulting in no measured voltage output.
When pressure is applied, the diaphragm takes up a bell shape. This causes strain on the strain gages. The inner pair of gages undergo compression while the outer pair experiences tension, as depicted in Figure 1. This change in strain causes a corresponding change in the electrical resistance in each arm of the circuit, leading to instability of the Wheatstone Bridge and the appearance of a measurable voltage across it, which is the output.
.jpg)
Figure 1. Bell shaped deflection of strain gage sensor.
Obviously, the degree of deflection depends directly on the pressure applied. This in turn reflects as increasing strain on the foil gages and increased resistance across the circuit. Thus the voltage output is a function of the diaphragm’s deflection, and the Viatran foil strain gages assess the applied pressure by measuring the output voltage of the bridge.
The bonded foil strain gage is extremely reliable and robust among the sensing technologies currently available. It is suited to very high pressures from 0-100 all the way through 0-100 000 PSI. It can withstand shocks, vibrations and pressure cycling with its rugged build. Temperature compensation is not required because of the fine accuracy with which the strain gages can be matched before they are bonded.
The primary disadvantage of this technology is its impaired performance under very low pressures, such as below 0-100 PSI. This is because at such a small range the diaphragm has to be so thin that the strain gages are sufficient to impede its motion in response to applied pressure, modifying the output.
.jpg)
Figure 2. Strain gages on a machined sensor.
Silicon Piezoresistive Sensors
The silicon piezoresistive sensors are based on a somewhat similar principle to the above, but utilize silicon chips embedded within a thin silicon diaphragm. These piezoresistive chips generate strong signals even at low pressures and therefore have a wider range as well as higher sensitivity.
This technology has been exploited by Viatran silicon piezoresistive sensors to make transmitters which are suited to pressure ranges from 0-2 up to 0-4 PSI. They are also ideal for sensing liquid levels.
The limitations of silicon piezoresistive sensor technology include its lack of sturdiness, which disqualifies it for applications that involve high impacts, shocks, pressure cycling or vibrations. The upper limit of pressure that can be sensed is also quite low, below 400 PSI, compared to bonded foil strain gages. Finally, it is more demanding to match these sensor chips accurately than it is to perform the same matching for foil strain gages, and therefore electrical compensation is necessary to keep the performance up to specified standards.
Ceramic Piezoresistive Sensors
Ceramic piezoresistive sensors are based on the use of conductive ink deposited on one side of a ceramic diaphragm, called the reference side. The ink fulfills the function of the variable resistors in a Wheatstone Bridge, corresponding to the foil strain gages in the first type of sensor. This technology gives a reliable and sensitive output in response to applied pressure in the lower ranges.
However, ceramic sensors are more durable than the silicon type and may be used at ranges of 0-15 up to 0-1500 PSI. Another benefit is the compatibility of the ceramic wetted parts in applications which are not suited for metallic wetted parts as when corrosive fluids are to be measured for their levels. This type of sensor is also more cost-effective.
Some limitations are obvious, including the low upper pressure limit due to the molecular structure which means that ceramics burst when overpressured without any sign of yielding beforehand. This means that the application of excessive pressure on a ceramic sensor leads to a dramatic burst failure, rather than the gradual distortion undergone by a metallic sensor in similar situations. The latter can therefore be reused because of its elastic nature, but not the overpressured ceramic sensor. Thus any application in which shocks or vibrations or rapid fluctuations in pressure occur is not suited for the use of ceramic piezoresistive sensors.
Finally, it is difficult to match and bond ceramic strain gages to the same degree of precision possible with foil gages, and therefore electrical compensation becomes necessary to achieve the same level of performance as per specifications.
Variable Capacitance Sensors
Variable capacitance sensors work on a different principle from the first three. It depends upon the variation in the capacitance of a pair of plate capacitors which is directly proportional to the applied pressure. It is ideal for measuring pressure differences in situations that have liquids on both sides of the sensor, termed “wet-wet” pressure input processes.
.jpg)
Figure 3. Typical variable capacitance sensor (cross section).
The advantages of this technology are obvious in measurement sensitivity at low pressure ranges. Viatran differential pressure transmitters make use of variable capacitance technology as do the Viatran gage-type and absolute pressure sensors.
The Viatran range of variable capacitance pressure sensors uses three metal diaphragms, of which the outer two are the wetted surfaces, lacking a spring constant and acting as passive diaphragms. They are separated by a silicon oil fill which contains two ceramic plate electrodes, both coated with conductive ink, as well as a third diaphragm which is the active diaphragm
This inner diaphragm is pulled tight during manufacturing, and thus has a spring constant. It is joined by hydraulic coupling to the outer diaphragms through small holes in the plate electrodes.
A charge is first produced between the inner or active diaphragm and the electrodes, so that two capacitances are formed, between each electrode-inner diaphragm pair. Provided the outer diaphragms experience equal pressures, the inner diaphragm remains undeflected, keeping the capacitances equal.
Once pressure is applied on one side, the wetted diaphragm deflects inwards on the side with the greater pressure. This results in more oil being forced through the holes on the electrode plate to impinge upon the inner diaphragm from that side, thus transferring the pressure on the outer wetted diaphragm to the inner diaphragm which thus bends towards the opposite electrode.
The capacitive storage in this case is proportional to the distance between each electrode-inner diaphragm pair, which leads to a higher capacitance developing between the inner diaphragm and the farther electrode. The variation in capacitance in turn reveals the difference in the pressures being exerted on both sides.
The advantages of variable capacitance pressure sensors are numerous and significant. Firstly, this technology yields high sensitivity to even tiny variations in pressure, such as that exerted by 1 inch water column pressure. Secondly, the outer passive diaphragms react to pressure by forcing oil through the small holes on the electrodes, of which there is little, thus preventing the possibility of severe deflection of the active diaphragm to the point of failure.
Thus Viatran variable capacitance pressure transmitters are designed to respond to small pressure variations sensitively but without causing rupture of the diaphragm, as well as obviating the need for recalibrations every now and then by simply preventing too much pressure on the active diaphragm. This type of sensor is therefore ideal for any applications in which there is a risk of high pressures which could otherwise lead to sensor failure.
On the other hand, the cost of such technologies is greater than the other types, and may create more noise signals when contrasted with the three types of sensors discussed earlier.
In all four sensor types, the output signals may be amplified or conditioned if they are at low levels to reach high-level outputs, such as 0-5 volts, 0-10 volts, or 4-20 mA.
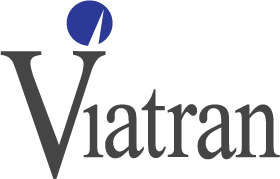
This information has been sourced, reviewed and adapted from materials provided by Viatran.
For more information on this source, please visit Viatran.