Food processing facilities producing products like baby food, condiments, tomato paste, cake mixes, and so on use batch processes in their production facilities. This means that the operator starts with an empty vessel and produces the end product by adding ingredients.
.jpg)
It is necessary for the operator to know how much of the given ingredient is to be added. This can be easily performed using point-level measurement switch(es) with control points at the fill point for every ingredient. This commonly requires installation of multiple sensors — one for every control point.
This type of application is more difficult than you might think. First, the sensor should have a hygienic design that can be easily Cleaned in Place (CIP), due to the nature of the products that are produced. Most of these products are heavily coating, viscous materials that lead to the failure of various technologies, such as tuning forks and mechanical switches. The less powerful technologies could be damaged by the weight of a majority of these materials.
Additionally, a large number of processes are agitated, which causes extensive splashing and coating of the material. If the switch does not show the precise material level, the consequence could be a destroyed batch, expensive downtime, or possible overfilling that requires clean-up.
Level Measurement Technologies
An evaluation of the most common point-level technologies used for batch process control is given below.
Floats
Floats should never be employed for batch processes. The float can block or jam and prevent the switch from denoting a control point, as a result of the viscous and coating nature of the material. Although some floats claim to have a hygienic design, in reality, it is difficult to clean floats in place. Moreover, multiple floats are required (one for every control point), thereby increasing the installation cost.
Tuning Forks and Vibrating Rods
Usually, these food batch processes start with a quite clean liquid like water or milk, yet a viscous slurry is produced when more ingredients are added. This viscous material coats heavily, causing failure of vibration-type switches. The sensor can be damaged by heavily agitated slurries, leading to failure as with any other single-point control.
Conductivity Switch
Although conductivity switches have been used for batch process applications, these are infamous for false level indication due to material bridging between the active electrode and ground. Using conductivity technology, several sensing rods can be installed on one mounting for multiple control points. Yet, the close proximity of rods only results in the bridging problem.
RF Admittance MultiPoint Switch—The Best Choice!
The ideal solution for batch process control is Drexelbrook RF Admittance Multipoint II. It needs just a single sensing element to be mounted from the top of the vessel on a hygienic Tri-Clamp fitting. The 3A hygienically designed sensor is a steel rod with TFE or Kynar insulation and is developed for CIP processing. It does not have any moving parts that might block or wear out.
RF Admittance Cote-Shield driven shield circuitry does not take into account even heavy coatings on the sensing element, thus preventing false alarms. The Multipoint II comprises of three independent DPDT relays, and it is possible to set control points at any point along the vertical sensing element. The Drexelbrook Multipoint II provides the ideal solution for batch process control applications.
- No moving parts
- Designed to withstand CIP demands
- 3A designed hygienic sensing elements
- Cote-Shield circuitry prevents false alarms due to coatings
- Three control points on one vertical sensing element
Cote-Shield Technology by Drexelbrook
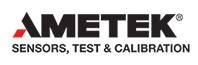
This information has been sourced, reviewed and adapted from materials provided by Ametek Factory Automation.
For more information on this source, please visit Ametek Factory Automation.