Applications Requiring Airflow Measurements
Measuring airflow is important for many HVAC, industrial and medical applications. Whether it is ensuring an air conditioning system is running smoothly or a hospital ventilator is providing the right amount of air to the patient, airflow measurements provide critical system feedback.
The number of systems that require feedback on airflow measurement is extensive.
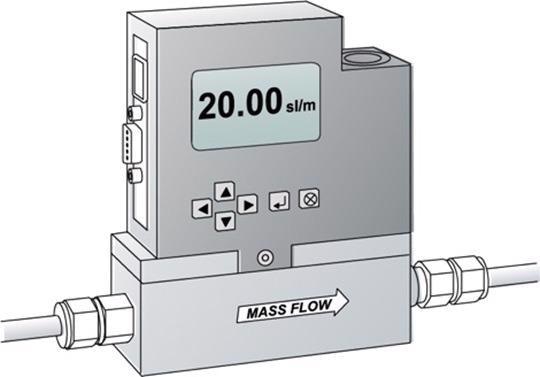
Image Credit: Superior Sensor Technology
Here are a few examples of the feedback provided:
- Air conditioning: Notifying of partial airflow blockages, such as through dirty air filters or clogged air ducts.
- Ventilators and Respirators: If the system is pushing too much (or too little) air to the patient.
- Clean and isolation rooms: Measure pressure to maintain a target low-pressure differential between the room being protected (or protected against) such that the net airflow is always in a specific targeted direction.
- Anesthesia, oxygen concentrators, nebulizers: To ensure the right mix of gases is being administered.
- Gas chromatography: If there is a decrease in flow rate signaling potential blockages in the line.
- Automobile engine: Measure the air entering the intake system to determine how much fuel to supply to the engine, to improve engine performance and efficiency.

Figure 1. Some Typical Airflow Applications. Image Credit: Superior Sensor Technology
The most common device for measuring airflow is a mass airflow sensor. However, in certain scenarios, a differential pressure sensor is a better solution. Let’s take a look at the two devices and their unique advantages.
Mass Airflow Sensors
A mass airflow sensor is a device with two pressure ports where air/gas flows from the first port to the second. Inside, there’s a sensing element with a heated surface.
As air or gas flows across the sensing element, heat is transferred. This creates a thermal imbalance proportional to the flowing mass. Note that the sensor is measuring the mass flow under standard conditions, not the actual volume of gas flowing through it.
While most sensors are compensated for the effects of temperature, changes in atmospheric pressure that affect the density of the gas may affect the output.
Thus, mass airflow sensors may also require an additional barometric sensor to compensate for variations in atmospheric pressure.
Finally, mass airflow sensors must be calibrated for a specific gas mix, as different gases have varying thermal characteristics. Consequently, mass airflow sensors are susceptible to errors when operating in an environment with changing gas mixtures.
Benefits mass of airflow sensors:
- As a thermal device, a mass airflow sensor is more stable at zero flow versus a differential pressure sensor.
- Mass airflow sensors have a higher output at low flows, resulting in better resolution at very low flows versus high flows.
Challenges with mass airflow sensors:
- Mass airflow sensor performance can be impacted by contaminants, such as dirt. If dirt enters the sensor, it can impact the air resistance and resulting output. Contaminants may also affect the heat transfer to the sensing element, which again would impact the output.
- Mass airflow sensors consume anywhere from 5x to 10x more power than differential pressure sensors. This can be critical for lower power and battery-operated devices.
- Due to the heating element, mass airflow sensors take a much longer time to stabilize on both power-up and during operation. Whereas a differential pressure sensor can stabilize within 1 msec, an airflow sensor can take up to 35 milliseconds. In addition, the frequency response of an airflow sensor can be 10x longer than a differential pressure sensor. These deltas can result in significant disadvantages in many time-critical applications, including medical and high-speed transportation.
- Mass airflow sensors may require an additional barometric sensor to compensate for variations in atmospheric pressure.
- Mass airflow sensors are susceptible to errors when operating in an environment with changing gas mixtures.
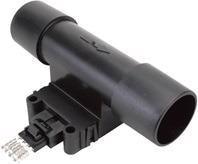
Figure 2. Image of typical mass airflow sensor. Image Credit: Superior Sensor Technology
Differential Pressure Sensors
Like a mass airflow sensor, a differential pressure sensor also has two pressure ports. But unlike the flow sensor, there is no gas flow between the two ports of a differential pressure sensor.
Instead, there is a diaphragm between the ports that measures the pressure difference between them. The two pressures to be measured are applied to opposite sides of the diaphragm.
The deflection of this diaphragm, either positive or negative to the zero state, determines the difference in pressure.
Differential pressure sensors have many uses and can be used to replace mass airflow sensors by measuring the differential air pressure across an orifice. As with any solution, there are positives and a negative in doing so:
Benefits of differential pressure sensors over mass airflow sensors:
- Unlike a mass airflow sensor, a differential pressure sensor is ‘dead ended’ so the only air/gas flowing into it is a small amount caused by air/gas compression or expansion under pressure. This structure reduces the possibility of contaminants impacting the output to only those cases where the flow through the tubing is completely blocked.
- A differential pressure sensor’s output is linear over its working range, so its resolution remains consistent at both low and high flows. A linear response is solely dependent on the type of flow restriction. It can be either a laminar flow element or a turbulent (non-laminar) flow element. For a laminar flow element, the delta pressure created as a function of changes in flow is linear. In the case of a turbulent flow element, the pressure response is a square root function and the dynamic range of the flow sensor suffers unless the pressure sensor has a very high signal-to-noise ratio.
- Differential pressure sensors consume anywhere from 5x to 10x less power than airflow sensors. This can be critical for lower power and battery-operated devices.
- As discussed above, differential pressure sensors can stabilize as quickly as within 1 millisecond during power-up and have a frequency response rate that can be up to 10x faster than mass airflow sensors. These are significant advantages for life-critical and time-critical applications.
Challenges of differential pressure sensors compared to mass airflow sensors:
- Since a differential pressure sensor is not thermal, it is not as stable at zero flow. However, some applications allow an auto-zero function to be included when there are known times where there is zero flow through the sensor. Another method to improve the near-zero flow reading is to include the use of a zeroing valve where zero pressure is forced across the differential pressure sensor for intermittent zero re-calibration cycles.
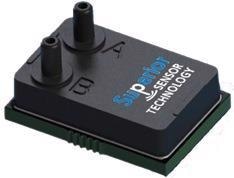
Figure 3. Superior’s Differential Pressure Sensor. Image Credit: Superior Sensor Technology
Superior Sensor’s Unique Differential Pressure Sensors
Having an extremely low noise floor, Superior’s differential pressure sensors are ideal for precise air flow measurements.
However, the advantages extend beyond the low noise floor. Some of Superior’s application-specific building blocks provide additional benefits compared to mass airflow sensors.
Multi-Range TechnologyTM
Multi-Range technology allows one pressure sensor to operate at maximum performance over several different pressure ranges.
Unlike mass airflow sensors and other differential pressure sensors, Superior’s Multi-Range allows pressure ranges to be changed ‘on the fly’ so that one device in the field can be used to serve multiple purposes.
Advanced Digital Filtering
One of the biggest impediments of differential pressure sensors is the errors caused by the noise generated from fans, blowers and other elements.
Utilizing an integrated advanced digital filtering technology, Superior’s pressure sensors eliminate the noise created by these factors prior to their reaching the sensor sub-system. Thus, the noise is eliminated before it becomes an error signal that can lead to inaccurate airflow reading.
Position Insensitivity
Superior’s unique dual-die implementation in our 210 models of sensors maintains consistent and highly accurate handheld readings regardless of the physical orientation of the end device.
Fastest Response Times
For time-critical applications, the interval in which it takes the pressure sensor to update its measurement data is vital. The faster you receive updated pressure measurements, the more accurate your output. While user-configurable, Superior’s sensors support update rates as fast as 1 millisecond.
Excellent Long-Term Stability
Long-term stability is defined by the maximum change in zero signal and output span signal of a pressure sensor under reference conditions within one year. This value is of greater importance in low-pressure ranges as the effect on the signal is stronger.
Factors such as temperature and mechanical stress can have negative effects on long-term stability. Superior has market-leading long-term stability measured typically within 0.15% of FSS within the first year.
Low Power Consumption
For handheld and other battery-operated devices, power consumption is another important factor in overall performance. With power consumption as low as 5 mA, Superior’s products will not adversely impact the battery life of even the most sophisticated equipment.
Download the full white paper
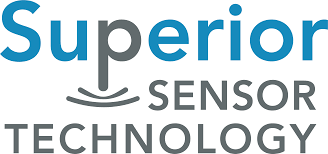
This information has been sourced, reviewed and adapted from materials provided by Superior Sensor Technology.
For more information on this source, please visit Superior Sensor Technology.