A closed-loop control system automatically regulates a process to the desired state based on continuous feedback from the system. It includes at least one electronic or mechanical device that is fine-tuned based on the feedback of the current state. Where necessary, the system can be adjusted to reach the preferred state.
Across many devices, closed-loop systems – often referred to as feedback control systems – are designed to achieve and maintain the preferred state autonomously without any human intervention.
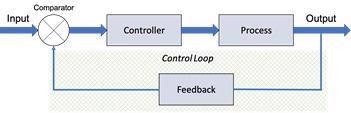
Figure 1. Basic Control Loop System. Image Credit: Superior Sensor Technology
Pressure sensors are frequently used to measure the flow or pressure in systems. It is often the case that under these circumstances, the sensor output is used directly as feedback in a closed-loop system.
Differential pressure sensors measure the density, level or flow of gas and air. They are often the key feedback component of many important systems in the industrial, medical, energy, automotive, aviation and HVAC fields.
Whilst many systems utilize the pressure sensor as the center of a control loop feedback system; they often use software as the external control mechanism. However, by using software, a higher speed CPU is needed that subsequently requires more power.
Furthermore, additional hardware is required, and the system is prone to injected system noise that can negatively affect sensor performance. To reduce noise, the sensor is run at a higher speed. There are several limitations to this kind of implementation, including:
- Cost: The extra components increase the bill of materials (BOM) of a product.
- Accuracy and Timing: More complicated feedback loops take longer to complete, resulting in a greater time lag that ultimately affects accuracy.
- Design Complexity: The overall product design is more complex and therefore requires a longer development period.
- Reliability: A product with a greater number of components subsequently has a greater number of potential failure points.
- CPU Requirements: Running the system requires a faster, higher-end CPU that produces more heat and requires more power.
The NimbleSenseTM Closed Loop Control Capability
Integrated into all of its differential pressure sensors, Superior Sensor Technology’s proprietary NimbleSense architecture combines processing intelligence with intelligent algorithms and signal path integration to make modular building blocks that are easily selectable to support numerous applications.
One building block component in NimbleSense is a closed-loop controller (CLC). This enables the company to integrate this function directly into specific sensor products.
This optional capability reduces the need to design and implement a complex control loop system. This subsequently results in better efficiency and reliability whilst reducing the cost of the products.
Superior Sensor’s CLC adds additional controls, allowing flow rates to be set and maintained via pressure measurement in the sensor. The CLC can directly control actuators, valves and motors to maintain flow rate targets.
Additionally, NimbleSense runs at a fast speed and has sophisticated filtering capabilities. This eliminates sensor-induced mechanical noise before it generates an error signal, preventing any adverse impacts on a system’s performance.
The integrated CLC design significantly decreases loop delays in the electronic circuit by up to 100.
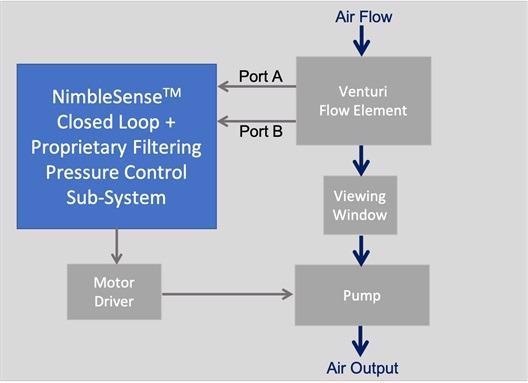
Figure 2. Closed Loop Control – Air Quality Application Example. Image Credit: Superior Sensor Technology
Figure 2 shows a block diagram of an implementation of the Superior Sensor CLC for an air quality application.
To efficiently measure air quality, maintaining a known/constant airflow through the viewing window is required. The differential pressure across the venturi flow element directly measures the flow into this viewing window.
The system establishes a target pressure level across the venturi. The differential pressure sensor automatically increases or decreases the drive to the pump. This maintains the targeted differential pressure, thus ensuring a continual airflow into the viewing window.
This is achieved by using the integrated NimbleSense closed-loop circuit. Additionally, it can also be used in combination with the company’s proprietary noise filtering, which can reduce loop delay by 100.
Summary of Benefits
The NimbleSense CLC capability can be valuable for many products, including, but not limited to, sleep apnea machines (CPAP, BiPAP, APAP), ventilators, anesthesia machines, oxygen concentrators, HVAC systems and flow meters.
In summary, the benefits of the NimbleSense integrated Closed Loop Control include,
- Significantly reduced loop delays which in turn increase responsiveness and accuracy of the product,
- Improved reliability of the product by eliminating discrete parts,
- Reduced overall system costs,
- Minimized system heat and power,
- Simplified product design,
- A faster time to market.
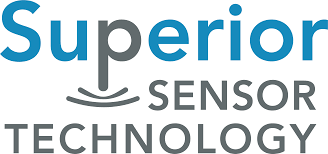
This information has been sourced, reviewed and adapted from materials provided by Superior Sensor Technology.
For more information on this source, please visit Superior Sensor Technology.