Columbia’s Foil Strain Sensors are more accurate than previous, less accurate counting accelerometer systems when measuring the fatigue stress encountered by aircraft under varied circumstances of speed, weight and mission configuration.
These sensors provide more precise monitoring of important undercarriage components and surfaces for possible fatigue damage caused by high-stress maneuvers, thousands of flying hours and landings. These sensors are also appropriate for normal laboratory applications due to their simplicity and dependability.
These sensors come with a variety of sensitive axis orientations to choose from.
The DTD2684 -1, -2, -3, -4, -5 sensors are flight-qualified and have been the industry standard since their introduction in the early 1980s. Models DTD2684-11, -12, -13, -14 have the same precision, robustness and convenience of installation but with a different sensitive axis direction.
Models for compensating materials typically utilized in aircraft structural production are available. The Columbia Model 5802 Strain Gage Amplifier is used to boost sensor readings and provide strain and temperature outputs.
Note: Exports from the United States are subjected to the Export Administration Regulations (EAR) and/or the International Traffic in Arms Regulations (ITAR) authorization procedures.
- Flight Qualified
- High Output — Two Active Arms
- Ease of Installation
- Choice of Sensitive Axis Orientation
Specifications
Operational
Table 1. Source: Columbia Research Laboratories, Inc.
Operational 1 |
Series DTD2684 |
Input Resistance |
1000Ω, ±2% |
Sensitivity |
1.025 (±1 %) mV/V/1000 μϵ |
Rated Excitation Voltage |
10.0 VDC |
Linearity |
±0.5% Max. |
Zero Offset |
±0.5 mV/V Typ. |
Operating Range |
-3500 to +5000 μϵ |
Output Resistance |
1000Ω, ±2% |
Sensitivity Shift |
±0.013%/°F |
Hysteresis, Repeatability |
±0.5% Max. |
Zero Shift |
±0.00025 mV/V/°F Typ. |
Creep |
<0.5%, 5 Min. @ 5000 μϵ |
Environmental
Table 2. Source: Columbia Research Laboratories, Inc.
Environmental 2 |
Series DTD2684 |
Temperature Range |
-54° to +125 °C |
Vibration |
30 g, 10 Hz to 2 KHz |
Humidity |
MIL-STD-202 Method 103B |
Salt Spray |
MIL-STD-202 Method 101D (168 Hours) |
Insulation Resistance |
100 Meg. min @ 500 VDC |
Dielectric Strength |
1050 VRMS, 60 Hz, 1 Min. |
Altitude |
Sea Level to 70,000 Ft. |
Flammability |
MIL-STD-202 Method 111A |
Shock |
100 g, 11 mSec |
Fluids |
Resistance to short term exposure to fuel, lubricating oils and hydraulic fluids |
Physical
Table 3. Source: Columbia Research Laboratories, Inc.
Physical |
Series DTD2684 |
Size |
0.560" x 0.560” x 0.150" Thick |
Encapsulation |
Silicone Rubber per MIL-S-23586A Type I, Class 2, Grade A |
Weight |
Approx. 13 gms (Depending on the length of the leads) |
Matrix |
0.001" Polyimide |
Leads |
#26AWG, Teflon Ins, SPC, 12" Min. |
1 @25 °C. 2 Installed Gage
Schematic Diagram
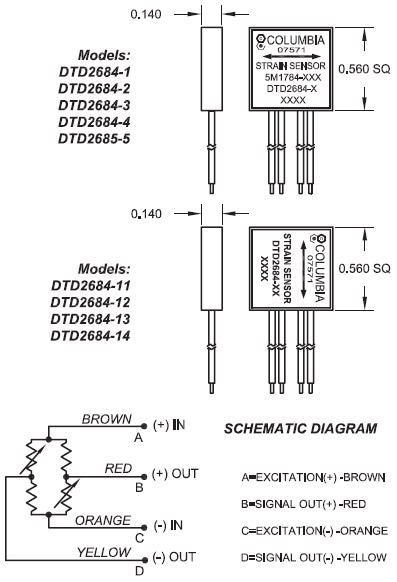
Image Credit: Columbia Research Laboratories, Inc.
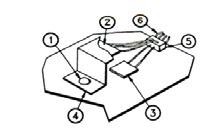
Typical Installation of Old Style Strain Gages. 1. Bolt or rivet removed from assembly; 2. Dummy gage(s) bonded to “Z Tab” of same material as structure; 3. Active gage bonded to structure under test; 4. “Z Tab” mounted to structure with bond or rivet; 5. Strain gage leads interwired and soldered to junction block; and 6. Entire unit covered with protective material. Image Credit: Columbia Research Laboratories, Inc.
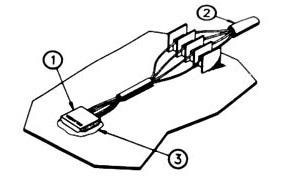
Installation of Columbia Strain Sensor. 1. Strain Sensor bonded to surface under test; 2. Leads connected to wire harness; and 3. Coat sensor and wires with waterproofing material. Image Credit: Columbia Research Laboratories, Inc.
Ordering Information (Note Sensitive Axis)
Table 4. Source: Columbia Research Laboratories, Inc.
Model |
Lead Length |
Compensating Material |
DTD2684-1 |
48" |
Aluminum 7075-T6 or 7050-T73651, IVD |
DTD2684-11 |
48" |
DTD2684-2 |
24" |
Steel, AISI 4130 or HP9-4-.20 |
DTD2684-12 |
48" |
DTD2684-3 |
48" |
Titanium TI-6AL-4V Annealed |
DTD2684-13 |
48" |
DTD2684-4 |
24" |
Carbon/Epoxy MMS 549 Type 1 |
DTD2684-5 |
48" |
DTD2684-14 |
48" |
Advantages
- Twice as much output
- A higher level of precision
- No compromise on structural integrity
- Installation time is reduced
- Optimal temperature compensation