Widely used in a host of industries, thermopile detectors are effective in conducting non-contact temperature measurements. Chemical processes usually necessitate the use of high temperatures but unfortunately, most thermopile detectors are unable to withstand temperatures above 180 °C. However, all this is set to change. Dexter Research has recently developed two thermopile detectors perfectly suited to all environments, including high-temperature conditions.
A vital requirement for a range of products and processes is the ability to gauge the precise temperature of materials and equipment. Close monitoring of temperature helps detect and prevent potential issues such as reduced efficiency, overheating and fires.
Many applications require non-contact temperature sensing, which can be crucial to prevent damage to the target or the sensor itself. Moreover, non-contact temperature sensors have a wide variety of benefits – they are often cheaper and provide faster data collection than contact sensors. A prime example of a non-contact temperature sensor is a thermopile detector.1,2
What are Thermopile Sensors?
Essentially, thermopile sensors are devices that aid in the conversion of thermal energy into an electrical signal. Comprising several thermocouples connected in series or parallel, they are used in conjunction with an infrared absorber membrane which converts infrared radiation into heat.
This thereby leads to an increase in the ‘hot junction’ of the thermopile. Further, the induced differences in temperature between the ‘hot junction’ and ‘cold junction’ result in the thermopile generating an output voltage minus any applied voltage bias. The voltage thus generated can then be measured in order to determine the target object’s temperature.1-3
Thermocouples and other temperature sensing devices generally measure the target temperature by relying on heat transfer from the target via contact. However, thermopiles can measure infrared radiation generated by the target remotely. Thus, thermopiles can conduct non-contact measurement of the temperature of all objects with a temperature above 0K, which generate infrared radiation. Thus, there is no need for external illumination while using thermopiles. Thermopiles can also be used to identify liquids or gases producing infrared radiation, thus facilitating a wide range of possible applications. However, erstwhile thermopiles were bulky, expensive, and needed complex integration, which limited their widespread availability and applications.1-3
MEMS Thermopiles: Superior Performance at Low Costs
Over the past few decades, there have been a series of new developments in miniature electronics. As a result, many devices today are now more compact, lighter, more economical, and deliver superior performance compared to their ancestors. Thermopiles too are following the same pattern, with miniature MEMS (Micro-Electro-Mechanical Systems) thermopile sensors now being widely used.2-4
Using micromachining to produce miniaturized electro-mechanical elements, MEMS thermopile devices are smaller in size and more compact and lightweight. Moreover, the manufacture of MEMS devices can be done batch-wise, thus lowering production costs. It is this factor that leads to MEMS thermopiles being small in size and low in cost but high on performance.2-4
Although not as sensitive as many other non-contact temperature sensors – such as bolometers and pyroelectric temperature detectors – thermopiles are extremely reliable and offer a significantly better cost-performance ratio. On the other hand, pyroelectric temperature detectors need elaborate cooling systems, making them larger, more complex, and therefore more expensive.5,6
In contrast, MEMS thermopile sensors are smaller and more economical. In addition, they provide low noise measurements and don’t require bias voltage or current. Inherently stable and with the ability to respond to a broad range of infrared radiation, MEMS thermopile sensors are thus the rugged, reliable choice for temperature detection and control. This explains their enormous potential in a variety of different applications, such as commercial, industrial and medical.2-4
MEMS Thermopiles: The Versatile Solution
As demonstrated previously, thermopiles can be used in a wide variety of applications across a broad spectrum of industries. In the home, thermopiles can be used as a device for controlling the temperature of equipment like microwaves, toasters, stoves, and tumble dryers. Thermopiles can also be used to monitor the temperature of circuits in devices such as PCs, laptops, tablets, and smartphones to prevent overheating. In the medical space, thermopiles are used in devices to monitor body temperature. Commercially, thermopiles can be used in safety control systems for fire and gas leak detection to protect against unsafe situations.1,3
Finally, industrial uses of thermopiles could potentially include chemical and biological processes, which require extensive environmental monitoring including temperature, liquid, gas, and heat flow detection. Thermopiles could be an ideal solution in the monitoring of industrial processes. However, the use of thermopile sensors in industrial applications is limited by the harsh environments required by chemical and biological processes, such as high operating temperatures.1,7-10
High-Temperature Applications of Thermopile MEMS Sensors
Monitoring devices in high temperature operating environments can be highly challenging. Firstly, many infrared window materials are incapable of tolerating high temperatures. Moreover, high temperatures can cause thermopiles to overheat and degrade, thereby resulting in permanently damaging the sensor.
As a result, despite the potential of thermoelectric sensors, most commercially available MEMS thermopile sensors can only operate in a somewhat narrow range of temperatures, ranging from -50 to 100 °C.7-10
However, some applications require specialist thermopile sensors that can withstand extremely high temperatures. For instance, automobile aircraft and propulsion systems require operation conditions from 300 to 800 °C and chemical production in the oil and gas industry involve temperatures ranging from 100 to 700 °C.
In many of these applications, in-situ temperature monitoring is vital for efficiency and quality control; as well as environmental analysis of hot environments such as hot spring mapping.7-10
Dexter Research’s Thermopile Sensors: Perfect for High-Temperature Environments
Dexter Research offers the world’s most extensive range of thermopile solutions. Recently, the company has developed two detectors that can withstand harsh, high-temperature environments. Dexter’s ST60 high-temperature sensors are tailor-made MEMS-based thermopiles that are designed to withstand temperatures of up to 300 °C. In other words, that is nearly 120 °C higher than its closest competitor!11
Thermopile sensors manufactured by Dexter Research offer unparalleled accuracy, heightened sensitivity, and unmatched rugged durability. Naturally, Dexter Research sensors are perfect for applications in military, medical, research, commercial and safety industries. Dexter’s ST60 high-temperature sensors have thus already found widespread applications in a host of industrial control applications.11,12
References and Further Reading
- ‘An Introduction to Thermopile Detectors’ https://www.azosensors.com/article.aspx?ArticleID=591
- ‘Infrared Detectors, Second Edition’ — Rogalski A, CRC Press, 2015.
- ‘MEMS-based thermoelectric infrared sensors: A review’ — Xu, D, Wang Y, Xiong B, Li T, Frontiers of Mechanical Engineering, 2017.
- ‘Review of micromachined thermopiles for infrared detection’ — Graf A, Arndt M, Sauer M, Gerlach G, Measurement Science and Technology, 2007.
- ‘Comparison of Pyroelectric and Thermopile Detectors’ — Neumann N, Banta V, Proceedings IRS² 2013.
- ‘Infrared detectors: status and trends‘ — Rogalski A, Progress in Quantum Electronics, 2003.
- ‘Temperature Measurement IR Sensors & Detectors’
http://dexterresearch.com/?module=Page&sID=temperature
- ‘Thermal Flow Sensors for Harsh Environments’ — Balakrishnan V, Phan HP, Dinh T, Dao DV, Nguyen NT, Sensors, 2017.
- ‘MEMS harsh environment sensor array-enabled hot spring mapping’ — Oiler J, Shock E, Hartnett H, Yu H, Sensors, 2013.
- ‘CMOS Compatible Midinfrared Wavelength-Selective Thermopile for High Temperature Applications’ — Zhou H, Kropelnicki P, Lee C, Journal of Micromechanical Systems, 2015.
- ‘ST60 High Temp: 300°C & 225°C Options’
http://dexterresearch.com/?module=Page&sID=st60-high-temperature
- ‘The World Leader in Infrared Thermopile Detectors’ http://dexterresearch.com/?module=Page&sID=about-dexter-research
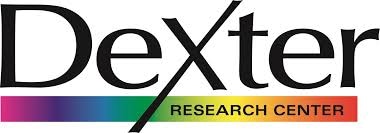
This information has been sourced, reviewed and adapted from materials provided by Dexter Research Center, Inc.
For more information on this source, please visit Dexter Research Center, Inc.