In many branches of industry, differential pressure measurements are used for a variety of measuring tasks. Apart from mechanical measurements using chemical seals or active pressure lines, there are now also electronic differential pressure measurements available.
.jpg)
Image Credit: VEGA
What, however, is the ideal solution for the user? The article below outlines the mode of operation as well as the differences between the systems. Its particular focus is on measuring accuracy, delivering support for the making of decisions and offering practical examples.
Operating Mode
Independent of its manufacturer, the mechanical differential pressure measurement operates at all times according to the same principle: two pressure values are applied to a differential pressure transmitter. Active pressure pipes, known as ‘capillaries,’ bring the process to the field instrument from the measuring point.
The difference is calculated mechanically by the measuring cell which is emitted, following transformation, in an electrical signal and output as a measured value.
The electronic differential pressure measurement is different. In this process, a master/slave sensor pair is used to measure the pressure values individually at the measuring points. The two instruments are connected electrically, and the difference in pressure is emitted electronically in the master sensor.
In the figure below, an example of level measurement in a pressurized vessel is provided to show the differences.
.jpg)
Mechanical (left) and electronic differential pressure measurement (right).Image Credit: VEGA
Applications and Operational Conditions
A typical application for differential pressure is the level measurement in vacuumed or pressurized vessels. These may be filling tanks in breweries, stock deaerators in the paper industry, reactors in the chemical industry or condensate collector tanks in power plants. Another area of application is the flow measurement in pipelines through orifice plates or pitot tubes.
Frequently, it is used in the generation and distribution of steam, as well as the production of biogas. Another widely used application of differential pressure measurement is the monitoring of any filter or function contamination, or the wearing of pumps, between the input and the output.
The operating conditions and requirements of pressure measurements can vary substantially: from minimum pressure differences of a few mbar, to high static pressures as high as 9.140 psi (630 bar); at process temperatures as high as 750 °F (400 °C); under extreme fluctuations in temperature; handling strong continuous vacuum, pressure and suction surges; and dealing with abrasion by the measuring medium.
.jpg)
Flow measurement via an orifice plate and mechanical differential pressure. The static pressure is measured by an additional sensor. Image Credit: VEGA
Selection of the Measuring System
The table below outlines how to find a suitable measuring system.
.jpg)
Tabular comparison of the mechanical (left) and the electronic differential pressure measurement (right) for certain criteria: [++] very suitable [+] suitable [-] unsuitable
Application Example in the Pharma Industry
.jpg)
Electronic differential pressure measurement of a master sensor in a distillation tank. Image Credit: VEGA
A distillation tank, which is around 80 ft (2.5 m) tall, is used to recover solvents for the active ingredient extraction via evaporation at between 120-140 °F (50-60 °C) in the high vacuum of approximately 0.75 psi (50 mbar abs).
Previously, mechanical differential pressure systems with chemical capillaries and seal systems were used with this kind of application. The filling oil was degassed and a measured value drift resulted, courtesy of the high vacuum and temperatures. The measurement quickly became unusable as it only achieved short service lives.
On the contrary, electronic differential pressure does not need any laying capillary lines. The oil-free ceramic measuring cell is also able to operate reliably in the long term in a vacuum and even at high temperatures without any drift.
Application Example in the Power Generation
So-called draft fans provide the combustion air for coal power stations. These are powerful axial fans. The air throughput has to be controlled and measured for the optimum combustion to be achieved within the boiler. In order to achieve this, numerous pressure measurements in a range of between approximately 0.4 to 0.6 psi (30 to 40 mbar) are necessary.
.jpg)
Electronic differential pressure measurement on a forced draft fan in a power plant. Image Credit: VEGA
Frequently, these are realized via differential pressure transmitters equipped with long pulse lines and small measuring ranges. This leads to a measured value drift, as a result of the influences of temperature and blockages by the formation of dust and condensation, as well as high installation efforts. Poor access during the frequently required maintenance operations is another disadvantage.
On the other hand, in the case of electronic differential pressure, the sensors are placed directly at the measuring points. The laborious laying of pulse lines is not required. More significantly, money spent previously on additional heating can be saved.
Long-term, reliable work is completed by the oil-free ceramic measuring cell without any drift, independently of the ambient temperatures. No maintenance or cleaning works are required on the sensor, courtesy of the ceramic measuring cell.
Application Example in the District Heating Network
.jpg)
Electronic differential pressure measurement on a compensation tank in a district heating supply. Image Credit: VEGA
A number of compensation tanks, which are approximately 70 ft (21 m) tall, assist the maintenance of pressure in district heating grids. These compensate for any leakages or temperature-related volume fluctuations which occur within the grid.
Until recently, the level measurement which was required was realized via differential pressure transmitters equipped with long capillary lines and flanges. These were placed outdoors and were equipped with an extra heating system. In addition, the installation of another sensor was required in order for the total pressure to be measured.
On the contrary, the other form of electronic differential pressure measurement is significantly simpler to handle and cheaper. Every one of the required measured values can be transferred to the control system. There is no requirement for an extra sensor in order to measure the total pressure.
Conclusion
Electronic differential pressure measurement provides an intriguing alternative to mechanical differential pressure measurement. In inhospitable conditions such as high vacuum, temperatures differences, abrasion, or in the case of any measuring points being economically reduced, this form of measurement excels.
Mechanical differential pressure measurement, on the other hand, remains the superior option at high static pressures or heavy pressure differences. The ideal form of measurement depends on the application in question.
Conventional and Electronic Differential Pressure | Pressure Instrumentation
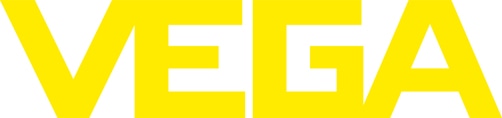
This information has been sourced, reviewed and adapted from materials provided by VEGA Grieshaber KG.
For more information on this source, please visit VEGA Grieshaber KG.